Your cart is currently empty!
Overview
Ethernet Pass-Through Demo Videos
Maple Systems MapleLogic PLC Pass-Through Demo Video
Allen-Bradley PLC Pass-Through Demo Video
This article provides information on how to PLC Pass-Through to any PLC device. The first example will be with a Maple Systems PLC. The second example will be with an Allen-Bradley PLC. PLC Pass-Through is available to any PLC device that is successfully communicating to a Maple Systems HMI.
Ethernet PLC Pass-Through is a powerful feature available within the EasyAccess2.0 and Utility Manager applications, enabling remote access to your PLC project from any location via an HMI. This functionality ensures you can efficiently manage and monitor your automation systems, regardless of your physical proximity.
Ethernet Pass-Through feature is available when both PLC and PC connect to HMI via Ethernet. Ethernet Pass-Through allows running the application on PC to control PLC through HMI. This feature is only supported on cMT / cMT X Series models.
Generally speaking, during Pass-Through, the HMI closes its connection with the PLC until the Pass-Through connection has ended. However, certain PLC drivers allow communications between the HMI and PLC in Pass-Through Mode.
Note*: Maple Systems supports 400+ communication protocols, download our “PLC Connection Guide” for more information.
Software Required
- EasyBuilder Pro – *HMI Engineering Application
- Utility Manager – *Local Passthrough
- EasyAccess2.0 – *Remote Passthrough
Software Dependent on PLC
- MapleLogic – *PLC Engineering Application
- RSLogix 5000 – *PLC Engineering Application
- RSLinx Classic Lite – *PLC Engineering Application
Hardware Required
- Maple HMI – *cMT/cMT X Series Only
Hardware Dependent on PLC
Demo Project Downloads
Network Topology
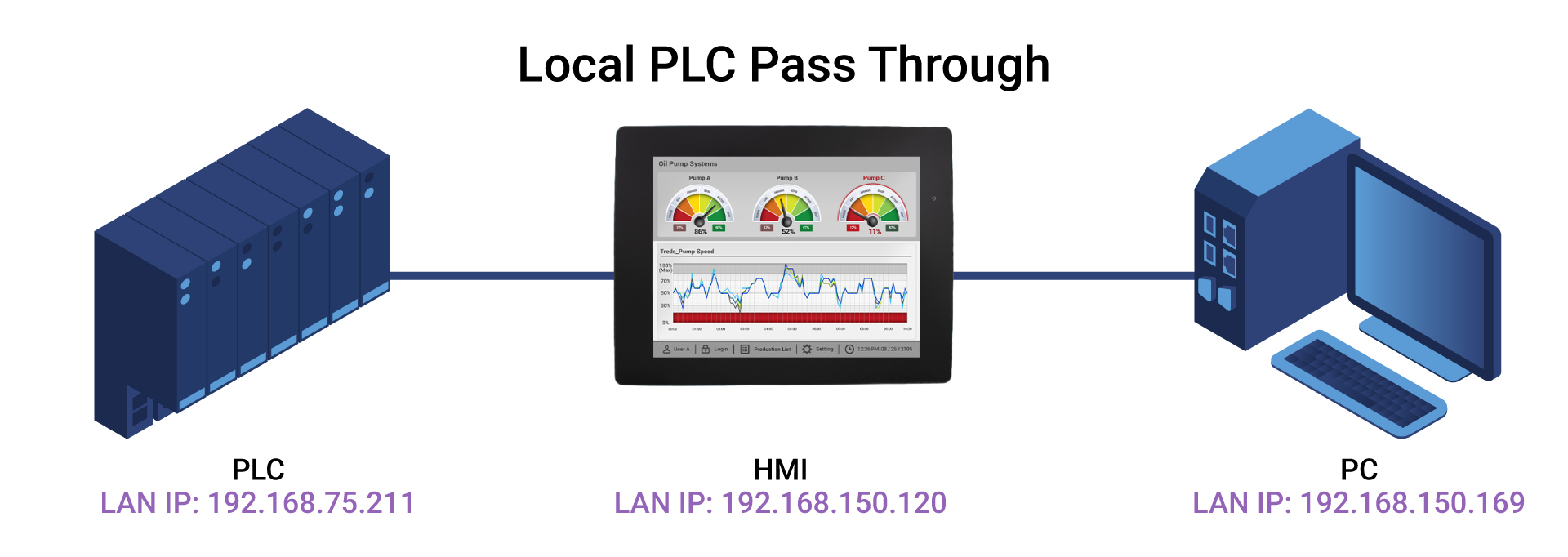
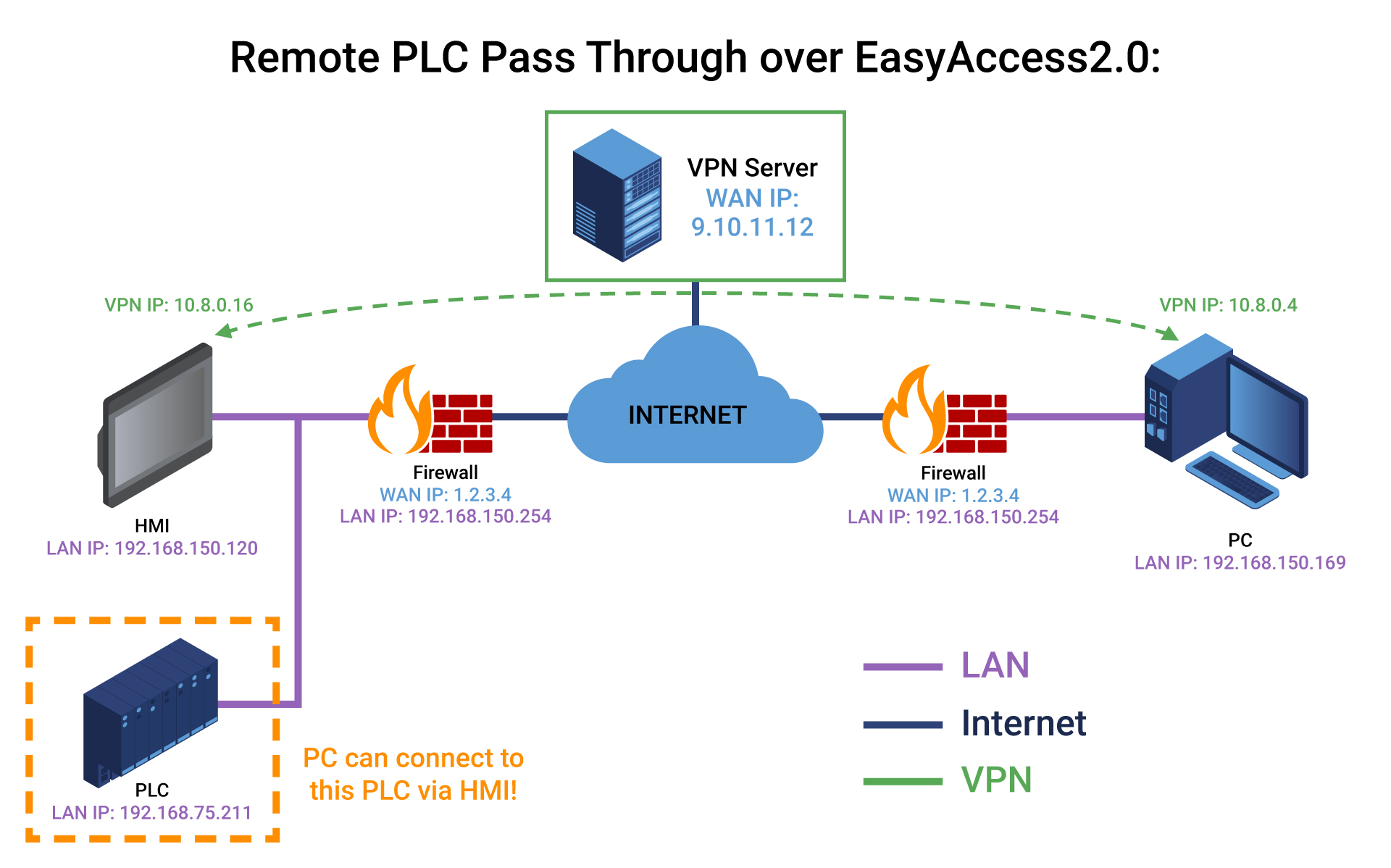
Demo Project Setup
EasyBuilder Pro
EasyBuilder Pro Demo
Launch EasyBuilder Pro
Inside EasyBuilder Pro create a new project. For this tutorial create a cMT2058XH project.
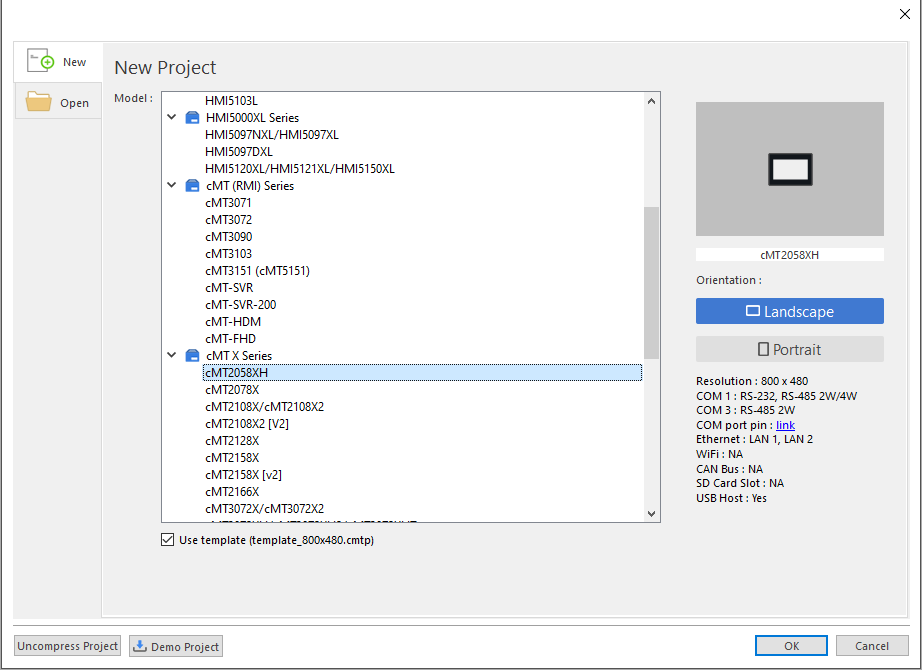
Inside the System Parameter Settings menu select [New Device/Server…]
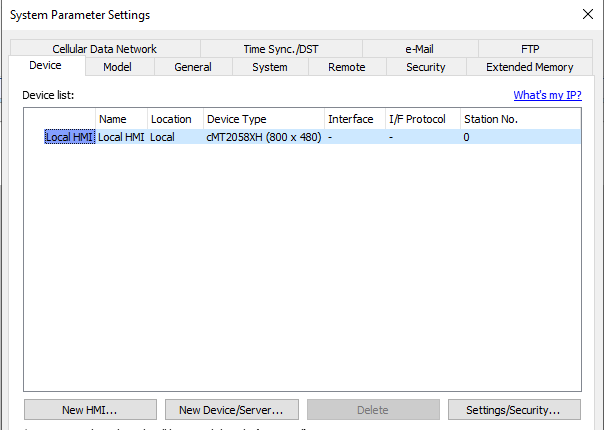
Select Modbus TCP/IP Master *PLC Passthrough works for all device drivers
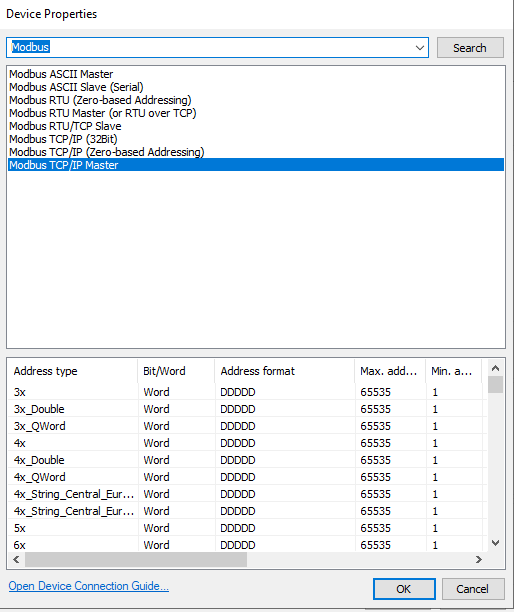
Configure the Modbus TCP/IP Master driver to have an IP address of 192.168.75.211
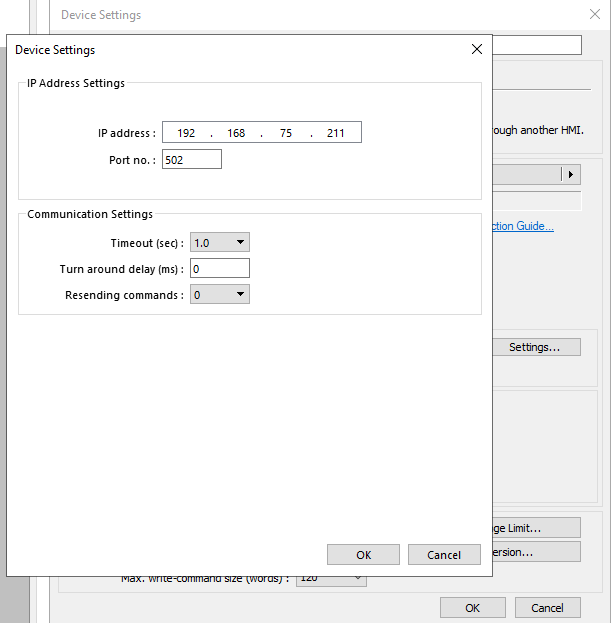
Confirm Modbus TCP/IP Master driver is configured correctly then exit out of the System Parameter Settings window by clicking [OK].
On the HMI configure LAN port 1 to be IP address of 192.168.150.120 and LAN port 2 to be IP address 192.168.75.10 with a subnet mask of 255.255.255.0 for both LAN 1 and LAN 2.
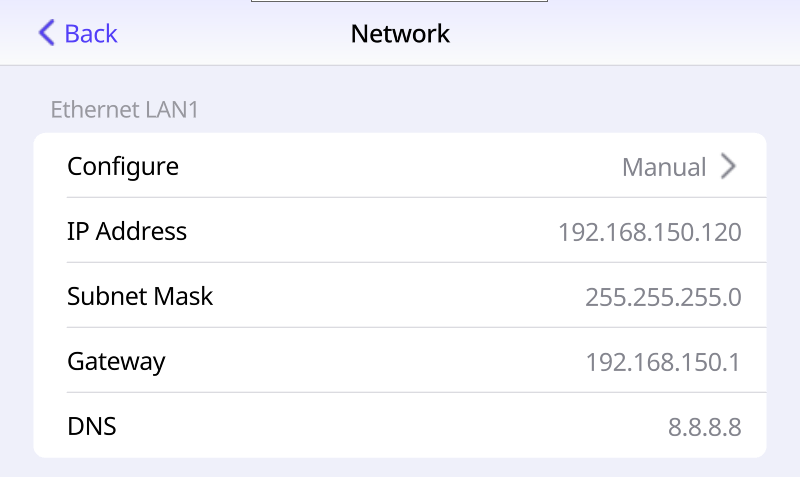
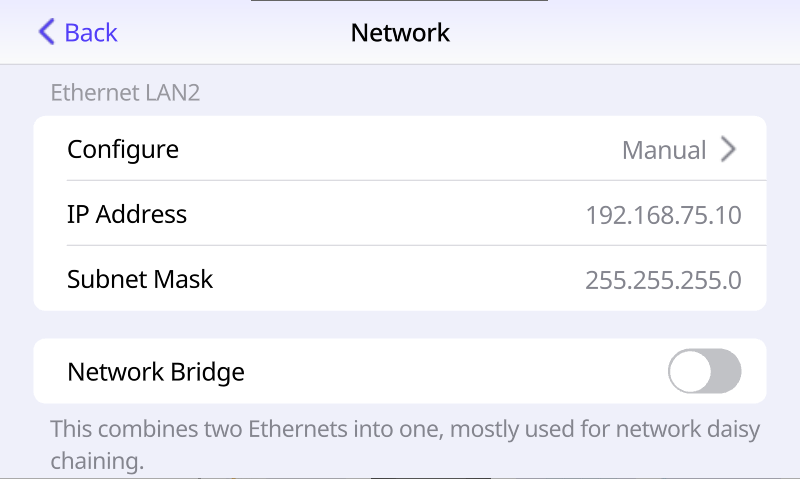
Inside EasyBuilder Pro navigate to the [Project] tab >> click [Download (PC->HMI)] >> select your HMI’s IP address on the Download window then click [Download].
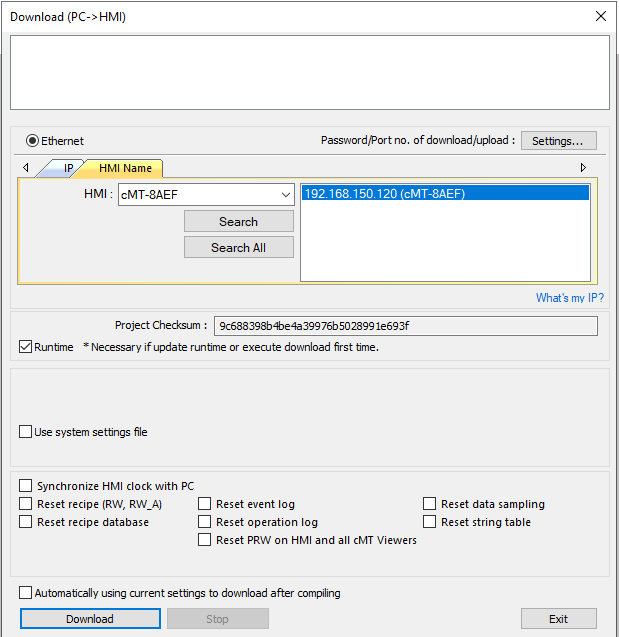
MapleLogic
MapleLogic Demo
Launch MapleLogic
Inside MapleLogic create a new project. For this tutorial create a PLC-ES project.
Select PLC-ES then click [Next]
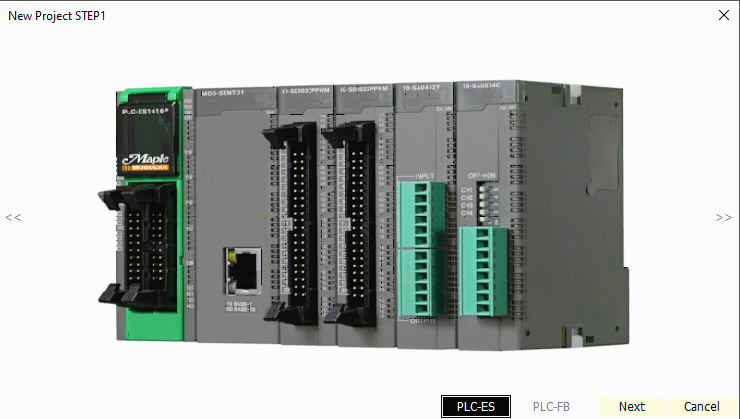
Provide a Project Name then click [OK]
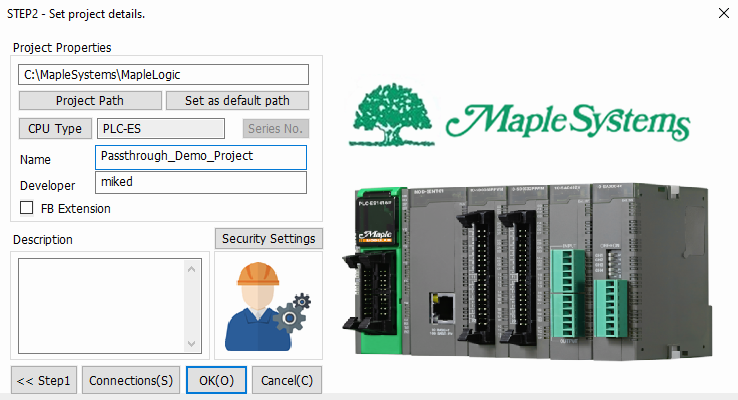
Click [PLC Parameter] and navigate to the [Ethernet] tab.
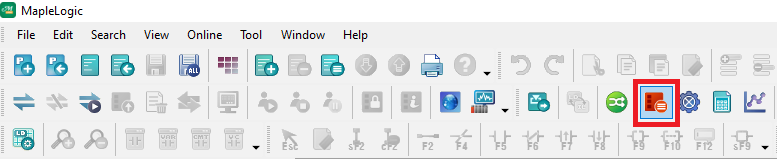
Insert the IP address of 192.168.75.211 with a subnet mask of 255.255.255.0 then click [OK]
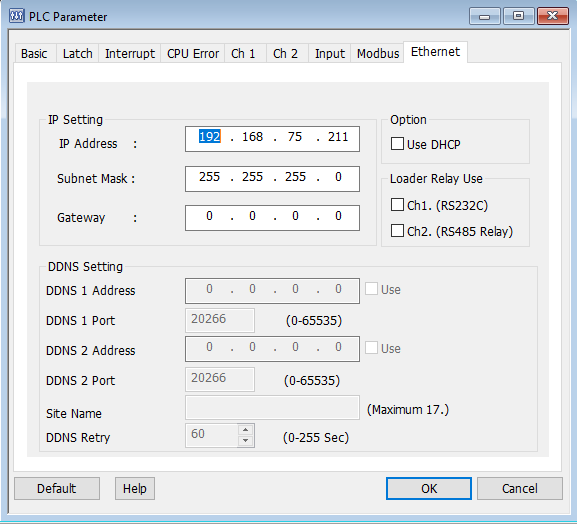
Click [Configuration] and download via [USB(U)]

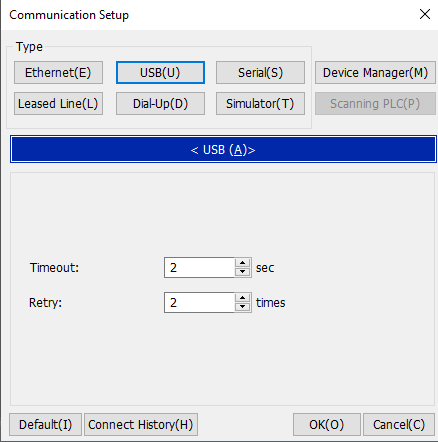
Create a basic Scan program before gong online. Right Click on [Program] in the [Project Window] and select [New Program]
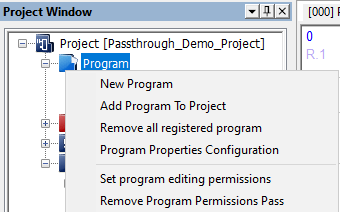
Give the Program a name, and select [Scan] for this demo project.
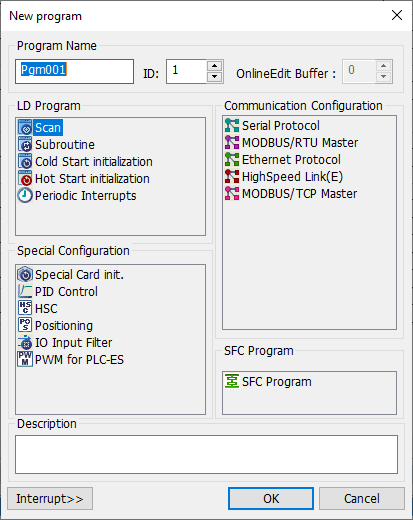
Create a similar [Scan] program, or download the MapleLogic_Demo_Project.
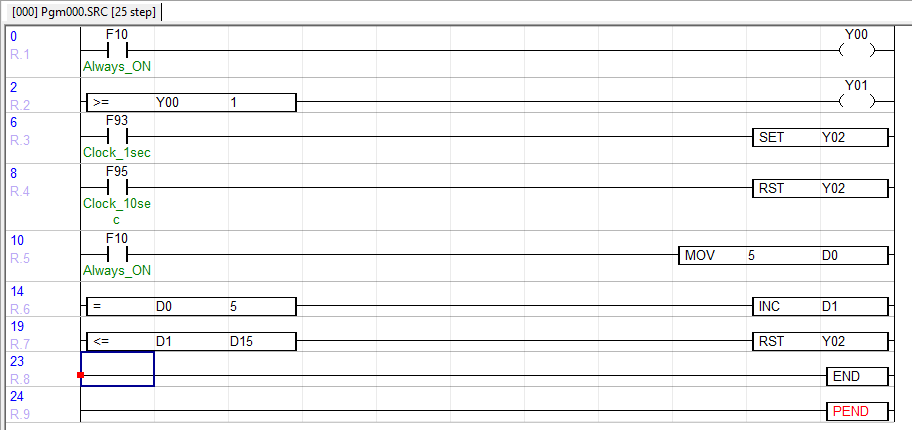
The IP address downloaded onto the PLC is now 192.168.75.211. You may download via [Ethernet(E)] using the IP address of 192.168.75.211.
Click [Link+Download+Monitor] to download via [USB(U)] to the PLC.
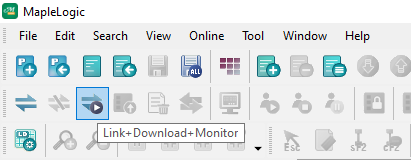
RSLogix5000
Allen-Bradley RSLogix 5000 Demo
Launch RSLogix 5000
Create a new project, or use an existing project. For this demonstration an Allen-Bradley CompactLogix L32E will be used.
Give your project a name, select a place for the project to be created in then click [OK]
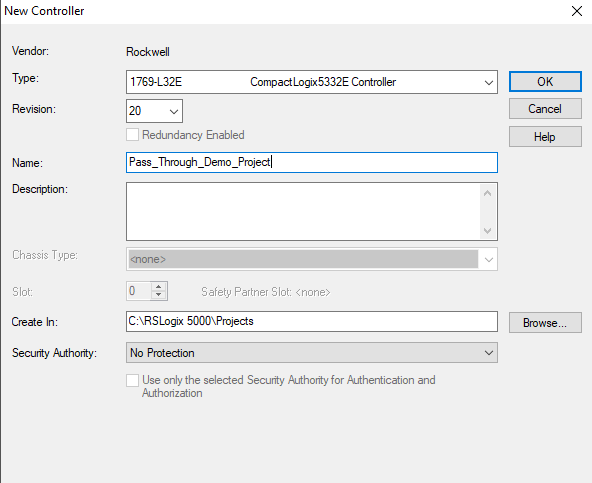
Assign your Allen-Bradley PLC an IP address of 192.168.150.228 and a subnet mask of 255.255.255.0 for example.
Inside RSLogix 5000 under Tasks >> open the MainRoutine menu and create some logic to download onto the PLC.
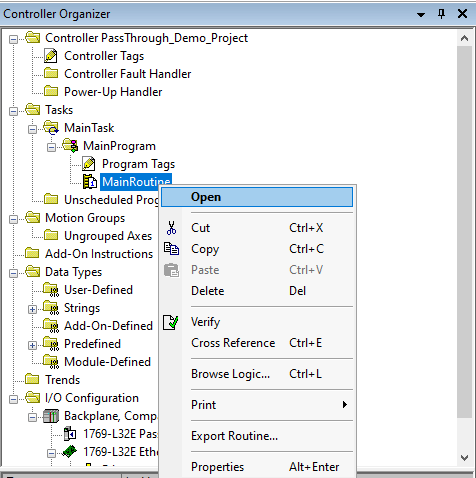

Download the created logic onto the PLC controller.
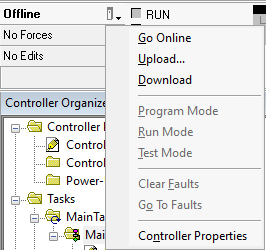
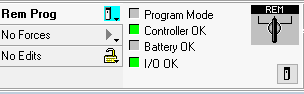
Local PLC Pass-through
Local PLC Pass-Through
Launch Utility Manager
Launch Utility Manager, select a cMT / cMT X Series model HMI, and then open Analysis & Testing tab
in which Ethernet Pass-through can be found.
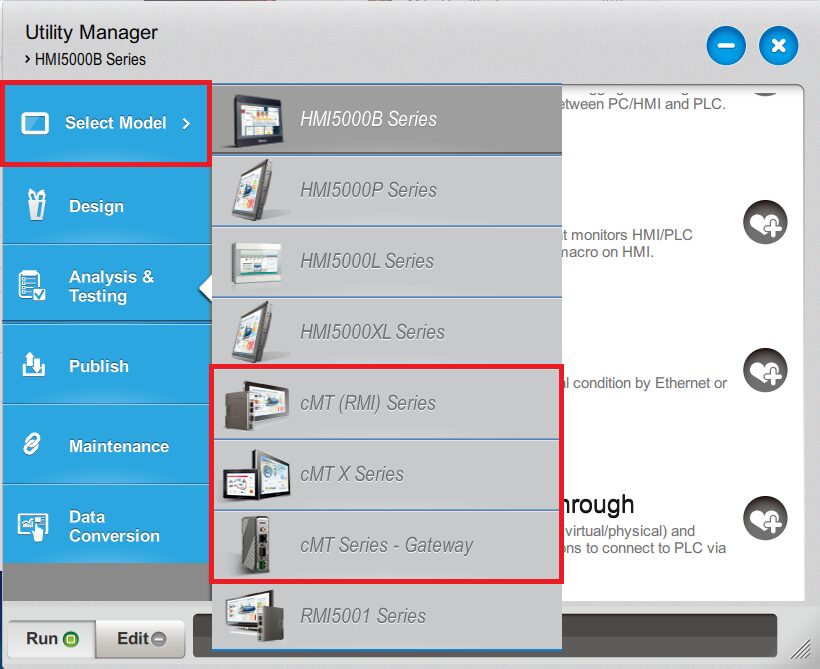
Navigate to the [Analysis & Testing] tab and click [Ethernet Pass-Through].
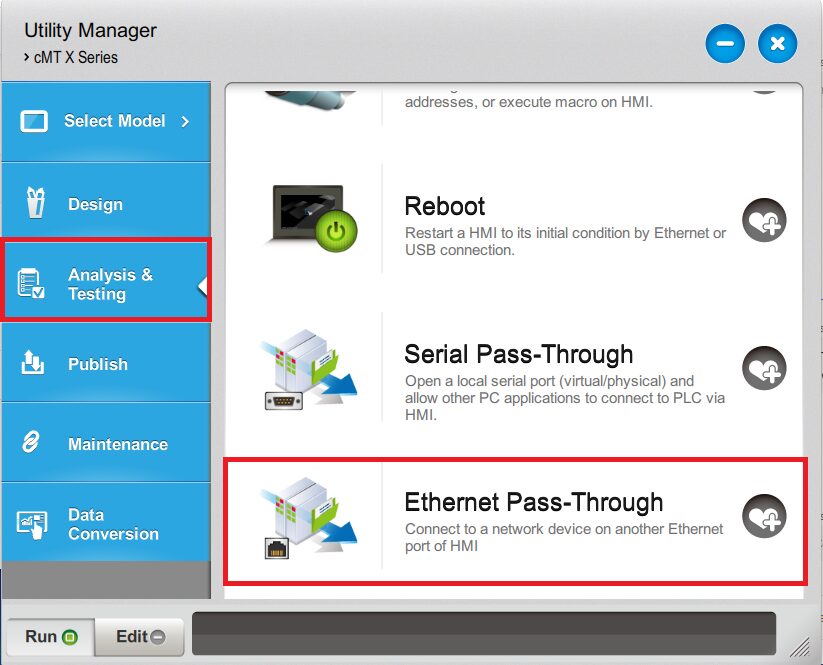
Fill in the communication parameters then click [Connect]
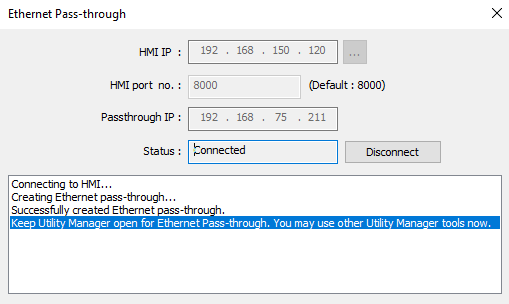
Inside MapleLogic click [Link+Download+Monitor] using the communication setup as [Ethernet(E)]
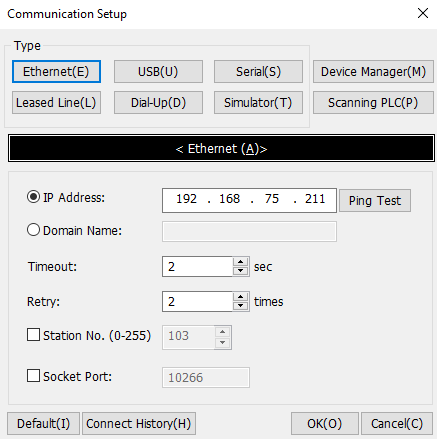
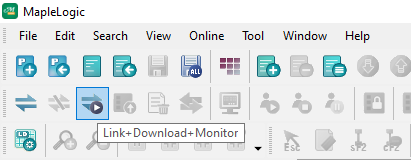
Usage
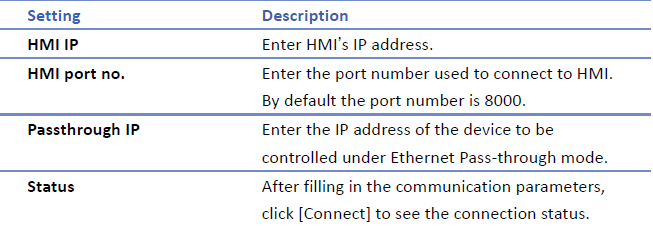
Notes
- Only one HMI can be used for the Ethernet Pass-through IP address
- Ethernet Pass-through feature is disabled when system register LB-9044 (disable remote
control) is ON.
Remote PLC Pass-through
Remote PLC Pass-Through
Launch EasyAccess 2.0
EasyAccess 2.0 not only makes possible direct connection to a Maple Systems HMI, but also provides Pass-Through function that enables the user to connect to the PLC on the remote HMI’s network. Consider an EasyAccess network as shown below where a PLC is within the same LAN network as the HMI. Here, the PC, by first establishing EasyAccess 2.0 connection to the HMI, may use the HMI as the relay and connect to the PLC as well.
Sign into your Domain as a user with VPN access privileges to an activated HMI unit.
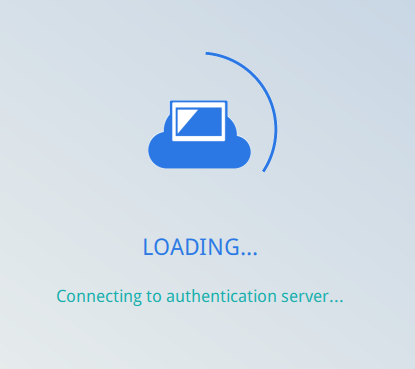
Click [Pass-Through] and enter in the IP address of the PLC unit: 192.168.75.211 then click [Set]
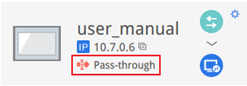
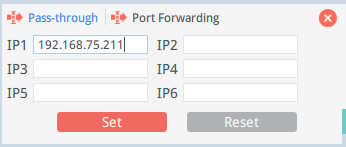
If the remote PLC and the local computer have the same private IP address range, a warning will appear, indicating that subsequent connection to the PLC’s IP address will be directed to the remote device instead of the local device if there is any.
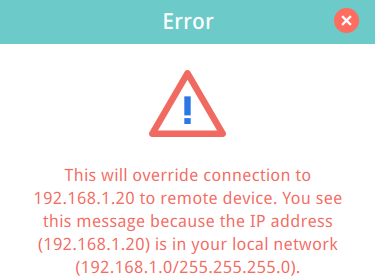
Additionally, Port Forwarding feature allows external networks to directly access corresponding internal devices. Up to six port forwarding configurations are supported.
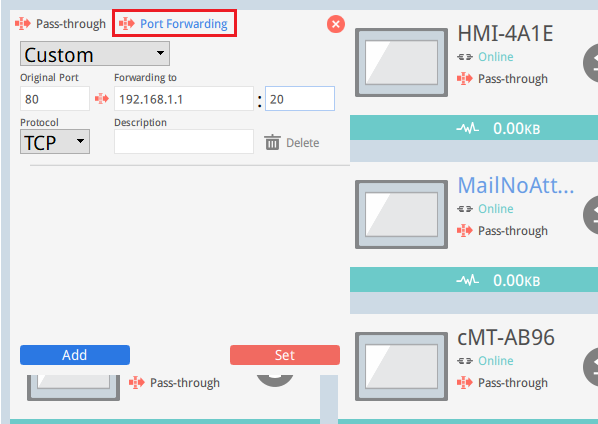
Establish a connection, once connected, the IP address of the PLC will be shown. The user may now launch the PLC Program.
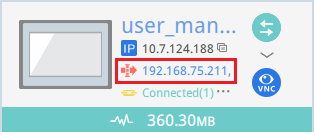
Inside MapleLogic click [Link+Download+Monitor] using the communication setup as [Ethernet(E)]
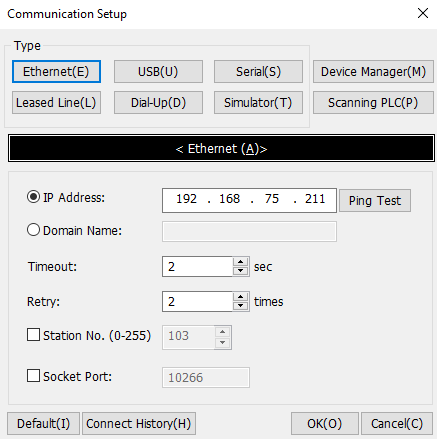
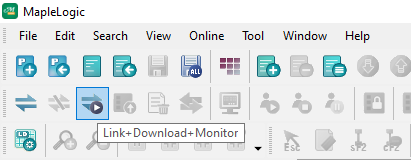
Conclusion
Ethernet PLC Pass-Through, available in EasyAccess2.0 and Utility Manager, empowers you to access and manage your PLC remotely via an HMI. This feature ensures that, no matter where you are, your automation systems remain accessible and efficiently monitored, providing peace of mind and enhanced control over your operations.
By leveraging Ethernet PLC Pass-Through, you not only gain remote access but also streamline maintenance and troubleshooting processes. This capability reduces downtime and enhances overall system reliability, making it an indispensable tool for modern automation environments. As your operations grow, the ability to maintain constant oversight and control will prove invaluable, ensuring your systems remain agile and responsive to evolving demands.
For more information, please reach out to Maple Systems Technical Support.
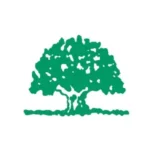
About the Author