Your cart is currently empty!
Overview
In today’s rapidly advancing industrial landscape, seamless communication between systems is crucial for optimizing efficiency and productivity. This article offers a detailed guide on connecting Remote IO to PLCs over Modbus, specifically focusing on the integration of a Maple Systems iR-ETNs with a Maple Systems Modular PLC using the Modbus TCP/IP communications protocol.
As you follow this guide, you will gain the knowledge needed to establish a reliable connection, which ensures seamless interoperability between your Maple Systems Remote IO and Maple Systems Modular PLCs, ultimately enhancing your industrial automation capabilities.
The iR-ETN firmware supports Modbus TCP/IP protocol. To ensure Connecting Remote IO to PLCs over Modbus is seamless.
Software Required
Hardware Required
- Maple Modular PLC’S – Any Maple Modular PLC can be used.
- MOD-SENT01-Ethernet Module
- iR-ETN Coupler – iR-ETN *used in tutorial
- iR-ETN Modules – DM16-N, DQ16-P, AI04-VI *used in tutorial
* The Maple Modular PLC DOES have Modbus TCP Master capabilities but you have to use the MOD-SENT01 Ethernet module perform this feature. In this tutorial, it will be an example using a Maple Modular PLC as the Modbus TCP Master device and a Maple Systems iR-ETN Remote IO as the TCP Slave Device.
Note: All of the Maple Modular PLC’s can be a Modbus TCP Master device by using the MOD-SENT01 Ethernet Module.
Network Topology
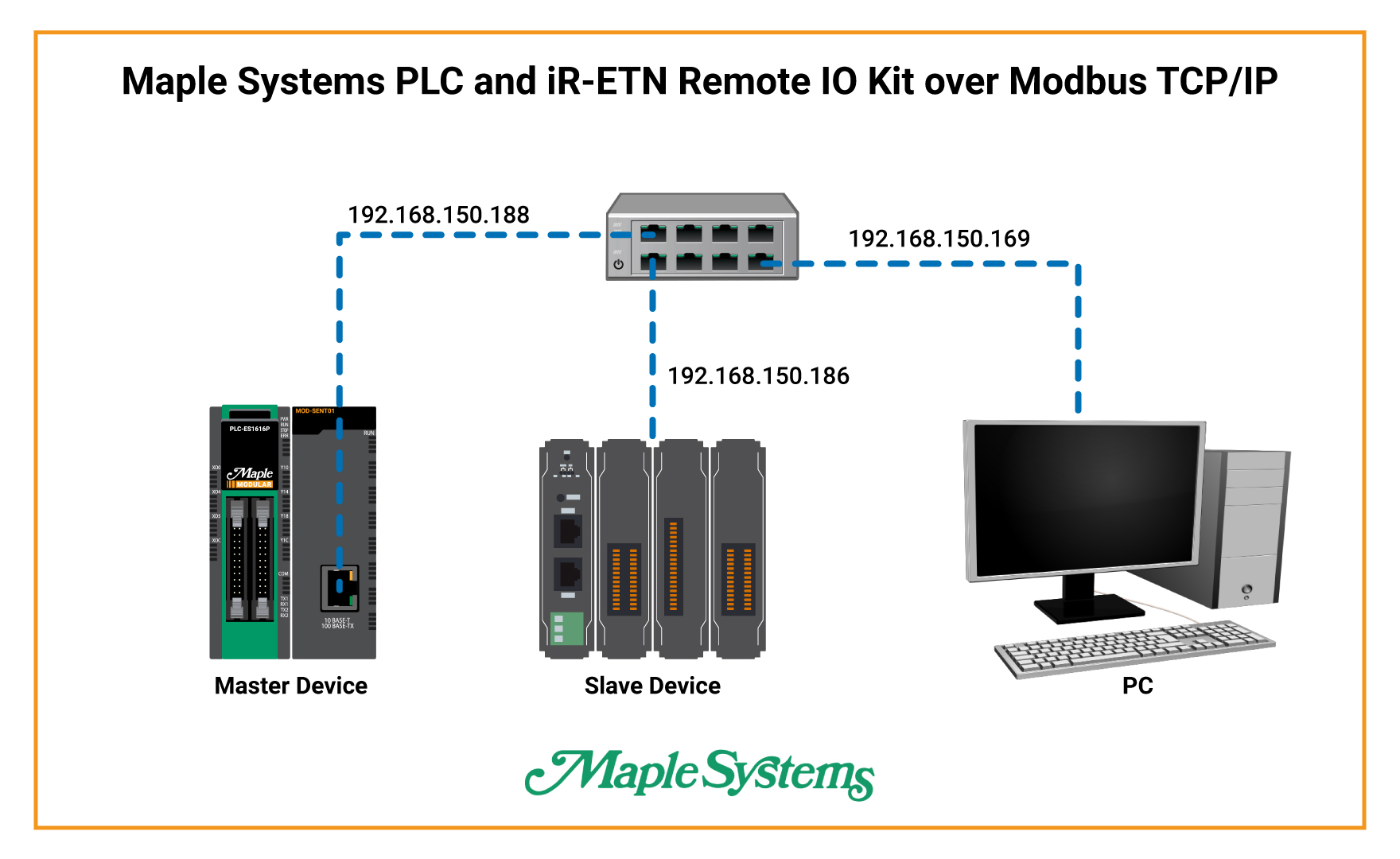
Remote IO Configuration (iR-ETN)
The iR-ETN firmware supports Modbus TCP/IP protocol.
Launch Remote IO
Inside Remote IO go to the Online tab and click [Automatic Scan] to scan the network for the iR-ETN coupler. The information of the iR-ETN and the connected modules is show as below.
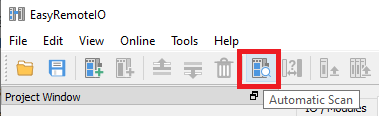
The default IP of a iR-ETN is 192.168.0.212. Please make sure the PC is on the same subnet.
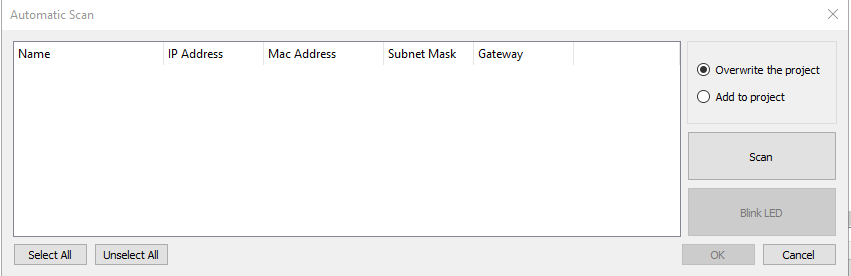
The iR-ETN can be found in Automatic Scan window. Select the iR-ETN you want to configure and click OK.
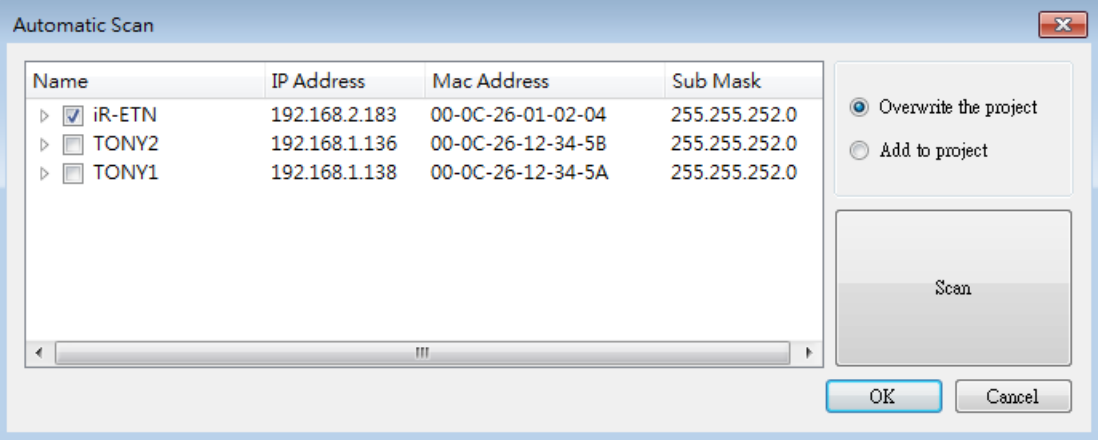
The iR-ETN and the module’s information will be shown as below.

Select [Change IP] under [Edit] to change the IP address of the iR-ETN and then click OK.
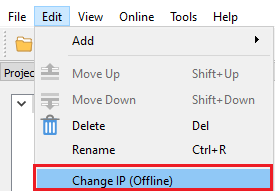
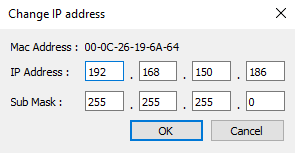
In the Project Window, select an iR-ETN and then go to the [Parameter] tab in the right column. Here you can change the related parameters of the iR-ETN. The actual value of the iR-ETN is in the [Online Value] column. The new value should be entered in the [Project Value] column.
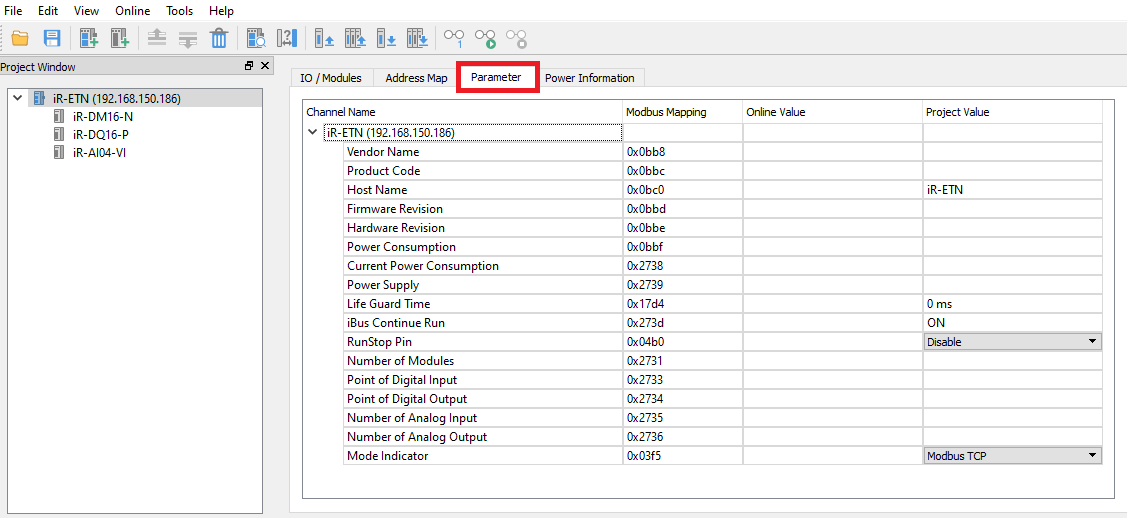
Click [Upload] to read the data from the iR-ETN coupler and present it in EasyRemote IO.
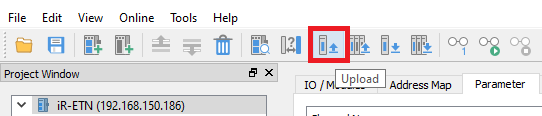
Click [Download] to write the data in EasyRemote IO to the iR-ETN coupler.
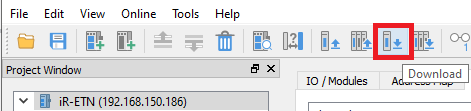
MapleLogic Configuration (Maple Modular PLC)
* The Maple Modular PLC DOES have Modbus TCP Master capabilities but you have to use the MOD-SENT01 Ethernet module perform this feature.
Launch MapleLogic
Create a new project and select PLC-ES as the CPU type.
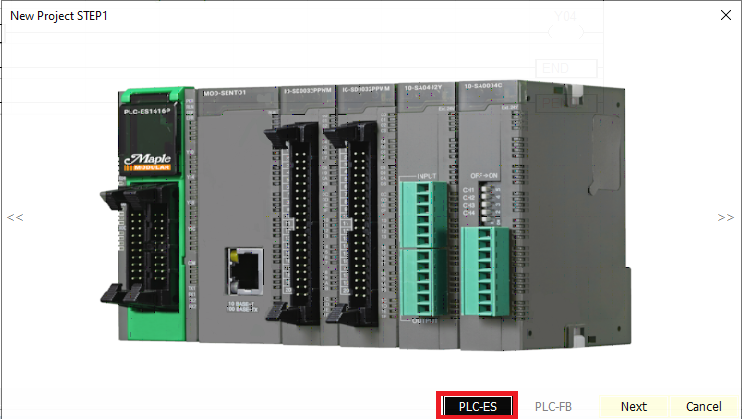
Right click on [Program] and select [New Program].
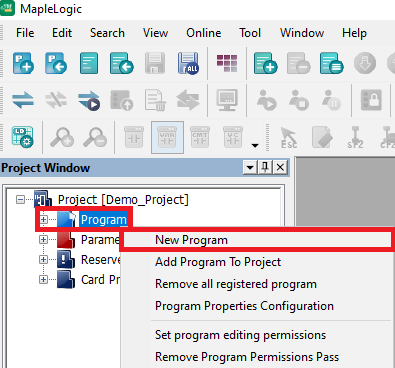
Select [MODBUS/TCP Master] under Communication Configuration. Name your program, and choose an ID number then click [OK].
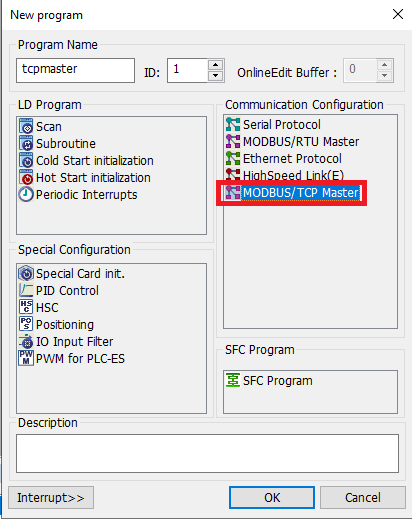
A Special Function window will open. Click [New] to enter the iR-ETN IP address then click OK. Ensure the slot number is configured to Slot1 then click [Save].
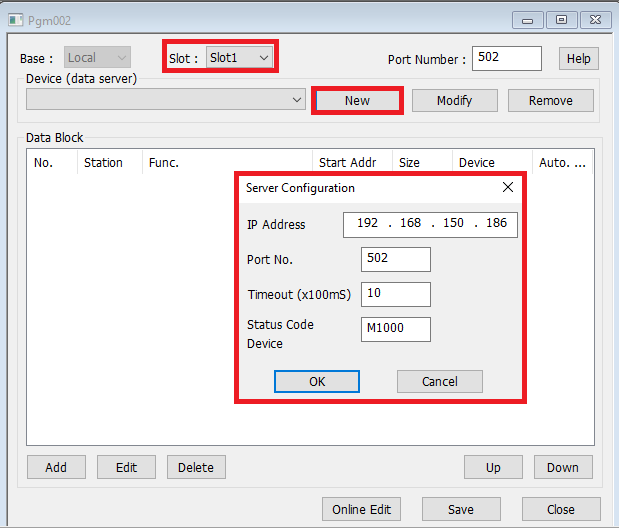
Next add a Data Block to communicate with the Analog Input Channel on the slave device. Click [Add] and choose the function “03 Read Holding Registers (4x)” with the Start Address of “2” click [OK], then click [Save].
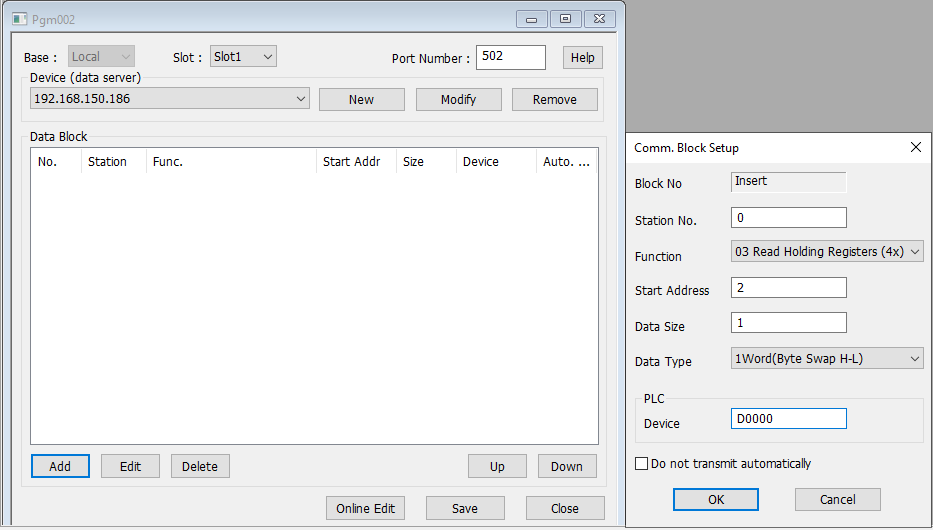
Now, configure the Modbus TCP Master IP address. Under [Parameter], click the [Ethernet] tab. Enter the Modbus Master IP address then click [OK].
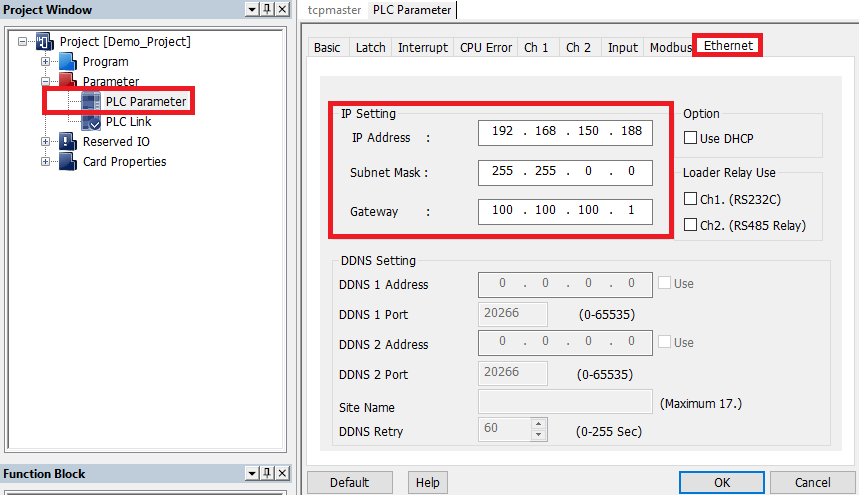
Lastly, configure the MOD-SENT01 Ethernet Module. To do so first, [Connect and Download] to the Maple Systems Modular PLC. Next, under [Card Properties] double click the MOD-SENT01 card. A Setup Ethernet Module window will appear.
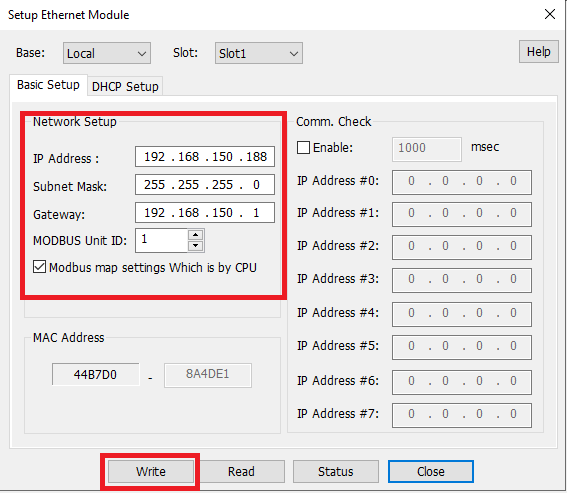
For Slot: select Slot1 as this is the slot number for the Ethernet Module. Ensure the IP address matches the TCP Master Device. Set the MODBUS Unit ID to 1 then click [Write] followed by [Close].
Demo Project
Configuring Logic
Using the steps above a project should have been created and downloaded for the Maple Systems iR-ETN coupler, and Maple Systems Modular PLC. Both devices should be communicating to proceed with this section of the article.
Right click on [Program] and select [New Program]. Select [Scan] under the LD Program column. Next, give it a Program Name, and ID.
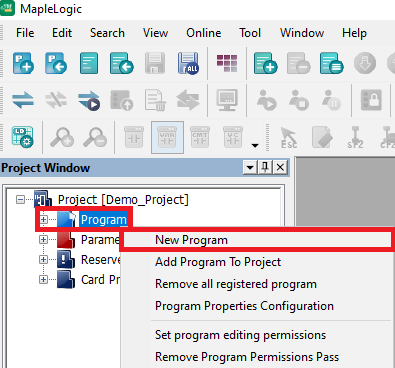
Inside the Special Function program add a Data Block to communicate with the Analog Input Channel on the slave device.
Click [Add] and choose the function “05 Force Single Coil (0x)” with the Start Address of “1” pointed at the PLC Device value of “Y0004”. Click [OK], then click [Save].
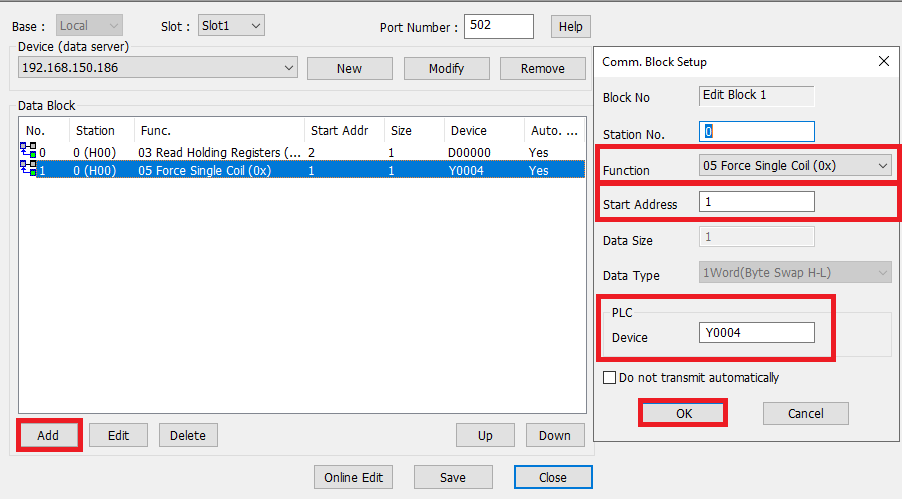
Right click on R.1 and insert a row above.

Next, double click the first rung block to place instructions. For this example type > into the field. This will generate a S1 is greater than S2 instruction where the S1 and S2 operands can be configured below.
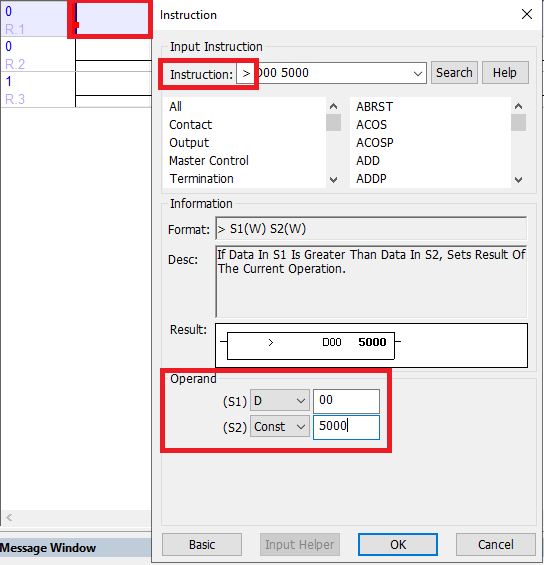
Modify S1 to be D with a value of 00, and S2 to be a constant with a value of 5000 then click [OK].
On the last rung block create a Coil pointed at the register-address of Y04.
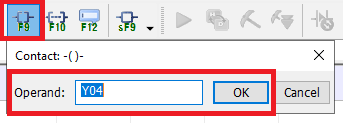
The first output on the iR-ENT’s DM16-N module will be turned on when the AI04-VI’s Analog Channel 1 is above the 5000 limit. For this example when the signal generator supplies 6.270mA.

Demo Project Download
Conclusion
In conclusion, connecting Remote IO to PLCs over Modbus is a valuable way to enhance the flexibility and scalability of your automation projects. The Modbus TCP/IP protocol natively provides a robust connection with up to 100 meters of distance between the PLC and the Remote IO, making it suitable for a variety of industrial applications.
Additionally, this distance could be extended even further with the use of network devices to meet the specific needs of your project. By implementing this setup, you not only streamline communication but also ensure that your systems operate efficiently, allowing for seamless expansion and adaptation to future demands. Whether you’re looking to improve your current setup or planning a new installation, the iR-ETN Remote IO offers a reliable solution for elevating your automation infrastructure.
For more information, please reach out to Maple Systems technical support.
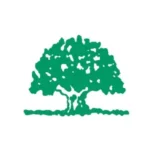
About the Author