Your cart is currently empty!
CODESYS
CODESYS provides a control solution that is one of the most complete implementations of the IEC 61131-3 standard for PLC software on the market. We now offer several innovative hardware solutions serving as the perfect platform for your CODESYS HMI or PLC project.
Combine the power of CODESYS with one of our CODESYS capable HMIs and Modular IO to create an innovative control solution that can tackle the most demanding applications. This unique architecture saves time, hardware cost, communication cabling, and valuable control cabinet real estate, without compromising on the CPU resources real time applications require. See our project examples below and get started building your solution today!
CODESYS Overview
CODESYS stands for Controller Development System and can be used for simple, or very complex, automation projects. As your project grows in complexity, CODESYS is capable of accomplishing many of those more sophisticated tasks, all within the CODESYS software platform instead of requiring multiple 3rd party applications or custom code engineers spend weeks perfecting.
Hardware Options
This innovative system is made possible by three components:
Hardware Platform

cMT3000X
Choose from one of the qualifying HMI models with an innovative multi-core CPU architecture. One processor is dedicated to running the CODESYS runtime while the other can run a full EasyBuilder Pro HMI application ensuring lightning quick graphics experience and real time PLC logic execution in a single platform.
CODESYS

CODESYS
A battle tested and complete PLC software package backed by a large userbase and development team, CODESYS fully implements the IEC 61131-3 specification. Implement your application in the programming language / editor of your choice. Use advanced object-oriented concepts to manage complex systems, and much more.
iR Remote I/O Modules

iR Remote I/O Modules
iR Remote IO modules. Easy to use reliable IO modules complete the connection to your field equipment. iR modules have three interface protocols to choose from: Modbus TCP, CANopen and EtherCAT all of which seamlessly integrate into your EasyBuilder Pro and CODESYS Projects. To these you can attach up to 16 IO modules. There are modules for any kind of system; analog, digital, temperature or motion control.
Getting Started
Ready to get started building your system? Here’s what you need:
Our documentation will guide you through the rest of the process:
- CODESYS Quick Start Guide
- Activate CODESYS
- cMT + CODESYS and Remote I/O Quick Start Guide
- Download sample EBPro / CODESYS projects
Example Setup:
As example consider creating a control system for a high temperature gas Kiln. The system requirements might include:
Documentation
Here’s the list of documents that support our CODESYS / cMT products:
Manuals & Guides
Sample Projects
Support Documents
Other Resources
- Weintek CODESYS package – This package should be installed as an add-in after you install the CODESYS development software.
Need Additional Support?
Additional Resources
We’ve compiled all of our most useful How-To’s, Troubleshooting, Webinar videos into convenient playlists.
Intro to EBPro
Learn how to create your first project in EBPro HMI programming software. Get a quick tour of the User Interface, Window Editing Pane, Sidebars, Menus, and more! Watch as our Product Trainer, Adam, creates a Tag and adds a Numeric Display to show a value on the HMI.
Smart HMI Series Overview
Maple’s Smart series is designed to meet the expanding need for new ways to connect to equipment, while preserving the core functions of a fixed operator terminal. Learn more about how our Smart HMIs make it easy to monitor/control industrial processes from remote devices.
More Information about the CODESYS / cMT Series – Smart IIoT Solutions
Application Solutions
Solution 1: Local Machine Control

New technologies bring new ways of interacting and controlling systems, but the need for a static HMI that is always ready and available will not go away. While cMT Series HMIs enable new and exciting features, the cMT Series also does not compromise on fulfilling this vital role.
The cMT Series uses EBPro, the next iteration of configuration software that Maple Systems customers use in our Advanced and Basic models. This software platform allows interface designers to select from over 300 protocol drivers and connect to nearly every PLC available in the automation market place today. With data from these devices, automation engineers can quickly construct state-of-the-art interface screens that present data to the operator in intuitive ways, so they’ll know exactly what’s going on within their machine. All of the standard display and data entry objects are available: buttons, meters, trends, alarms, and much more.
Once the project is designed, choose from one of our 4 Touchscreen cMT model sizes (7″, 9.7″, 10.1″, or 15″). These units can be mounted in a control panel like any traditional HMI. cMT Servers, which do not have a built-in display, can be paired with a cMT-iV6, a 9.7″ touchscreen display or a cMT-iM-21, a 21″ touchscreen monitor. Each can be a mounted in a traditional control panel. These screens provide a permanent fixed terminal that operators expect to find in any system. These screens provide a permanent fixed terminal that operators expect to find in any system.
Solution 2: Adding Remote and Mobile System Displays
A static, panel-mounted display is great for many applications but can be limiting in others.
For example, a machine may be quite large and the operators want to be able to stand directly in front of the section of the machine they are working on. Previously, the only way to accommodate this need would be to install a separate control panel at every point of interest along the assembly line. Or, a plant manager may want the ability to quickly log into any plant floor machine in order to respond to issues and monitor production rates. cMT Series HMIs allow you have it either or both ways.

Wireless Access to Remote Displays
The cMT Viewer application enables operators to use wireless Android, Apple, or Windows® tablets as their HMI. They are untethered from the control panel. The operator can move freely to any part of the assembly line or processing plant, taking their HMI with them. This eliminates the need for running back and forth to the panel while troubleshooting, or tying up two operators; one at the control panel pushing buttons, and the other at the machine troubleshooting equipment.
The cMT Viewer application can also be run on any Windows® PC – any computer on the same network as a cMT HMI can easily view and control the system. A plant manager can connect to any cMT HMI in their plant to get a real-time view of exactly what is occurring with that machine. The connection is password protected so only authorized users can have access. The Monitor Mode feature in cMT Viewer allows plant managers to view live data from up to 50 connected cMT devices simultaneously.
An alarm condition from any device would immediately alert the operator, enabling quicker response rates and resolution to the issue. The cMT Viewer application can run on a traditional Windows desktop or on panel PC to provide a supervisory control station with access to many subordinate machines.
Explore cMT Viewer.
Solution 3: Data Management
The HMI view of an operator interface terminal, whether on a local display, mobile tablet, supervisory panel PC, or remote workstation, is only one view of the important data in an automation system. There are also; alarm and data logging, database integration, recipe management, protocol translation and more. cMT Series Products prove to be a flexible tool in these areas as well. Let’s tour a few features available to manage your data on the cMT products:
Modbus Gateway
In an ideal world, every machine vendor and systems integrator would use the same protocol and all equipment would seamlessly communicate with everything else on a plant floor. More often than not, this is far from the case. As a plant grows over time and different systems are added, little thought is given to the process as a whole. You’ll often find different systems, from different manufacturers, speaking different protocols, on different serial busses. Fortunately, cMT products speak many languages. cMT Series Products can use over 300 protocols on any of the available com ports, and translate them to the default industrial standard protocol: Modbus TCP/IP. The cMT device becomes a transparent protocol translator, allowing upstream SCADA systems to connect to PLCs as if they were all using the same protocol on the same bus.
Modbus Communication Gateway

Database Object Increasingly, data that machines produce needs to be recorded and preserved. The data may be useful in process improvement or may be required by regulatory agencies. The cMT products have an object which allows them to log a data sampling object or an alarm log directly to an SQL database server over an Ethernet LAN.
This eliminates the need for manually retrieving and entering log files from each machine independently. Data from many different sources can be aggregated and stored in one central safe and secure location, automatically.
Databases and Recipes Recipes are a collection of parameters stored in the HMI that can be transferred to a machine with one press of a button. Different parts may require different amounts of material, different cook times and temperatures, or different processing steps. This data often needs to be shared across multiple machines that may be at different steps in the process, or may be redundant production lines working on producing the same or similar products.
SQL databases can act as a storage tank for all machines sharing a particular recipe database. cMT HMIs can query the database for current recipe data before sending those parameters to the PLC. This way, changes only need to be made to this central database, instead of manually changed in each HMI.
This feature saves time in systems that have many machines sharing many recipes. The changes, additions, and deletions to the database only need to be made in one place and are then automatically updated throughout the system. This ensures production uniformity throughout the system. A single machine will not get stuck using an outdated recipe simply because someone forgot to update it.
Solution 4: IIoT Gateway
So far we have seen how the cMT series of products work as a local display, a mobile HMI server, and a data manager within the factory. But the cMT series packs even more features that enable yet another level of access and control. The IIoT, or Industry 4.0, is a growing area of interest in the automation market. The cMT series provides a capable, ready, and secure solution for the IIoT.
Learn more about Maple Systems IIoT Solutions
OPC UA
Open Platform Communications (OPC) Unified Architecture (UA) is a tried and tested communication protocol supported by many SCADA, MES, and ERP software providers. The protocol has built-in security with signed and encrypted data transfer using state-of-the-art encryption algorithms. Data is organized into browsable objects, making it easy to both access data and quickly understand how to use what the data represents.
Any data accessible to the cMT can be added to the OPC UA server to be accessed by upstream devices. The configuration interface required to add data to the OPC UA server is very simple and straightforward to use. The user can organize data into multi-level objects with descriptive names. An OPC UA client device connecting to the cMT will see data organized in the same intuitive way.
MQTT
MQTT is a powerful and efficient IoT protocol that is lightweight, highly scalable, and has excellent support on many client devices and programs. MQTT integrates well with Amazon AWS, IBM Bluemix, and Microsoft Azure cloud hosting services for next level data collection and processing.
The cMT Series Smart HMIs offer a full featured MQTT implementation. An easy to use configuration interface allows the user to select data from any of the supported PLC drivers, add it to an MQTT topic, and publish it periodically or whenever values change. The cMT Series can also subscribe to MQTT topics and write the received data to internal HMI memory or to PLC memory addresses. And as well, cMT Series HMIs can host an MQTT broker internally, coordinating connections from other Maple Systems HMIs or any other MQTT enabled device.
cMT HMIs offer advanced integration with Amazon AWS’s Device Shadow service which creates a virtual representation of the actual device in the cloud. And EBPro supports the Sparkplug B MQTT payload specification for integration with Ignition SCADA software and other Sparkplug B compatible software programs.
The MQTT protocol is data agnostic, meaning that any data can be sent through the protocol, including plain text messages. This raises security concerns since anyone with access to the network can view the data in transit. However, the MQTT feature on Maple Systems products includes the ability to encrypt messages from publisher to subscriber. This ensures that messages are only read by the people and programs authorized to receive the messages.
Maple Systems-Wein Strategic Alliance
Maple Systems ‐ Weintek Strategic Alliance ‐ 2018
Maple Systems has been the #1 authority for Weintek products in the North American market for nearly two decades. We have evolved together over the last several years to provide powerful controllers designed to implement and maintain specific fundamentals, which are recognized today as industry standards.
Given that Maple Systems knows Weintek products inside and out, Maple is able to precisely administer in-house repairs and provide FREE, superior, local technical support to our customers. Our team is well-versed in the complexities of what makes these products outperform the competition in both capability and cost.
Maple Systems and Weintek Labs equally pride ourselves on not only having mastered the basics in our controls offerings but are also passionate about remaining at the forefront of technological changes in our market. Weintek Labs sets a precedent in keeping products relevant, compatible, easy-to-use, and above all, reliable ‑ is why Maple Systems is proud to be Weintek’s #1 provider in the US.
We invite you to explore the variety of HMIs, remote and smart devices available on our website today. Our 30+ years in the industrial automation field, our commitment to offering up-front affordable pricing and never charging for technical support are all reasons why Maple Systems remains an established name in an abundance of competition throughout the automation market.
For questions on any of our products or services, please don’t hesitate to call. You can also email sales or technical support directly at:
See also: Weintek Strategic Alliance
User Friendly HMI Configuration Software
Free, powerful HMI configuration software for our HMIs provides the flexibility to create and deploy custom control applications suited to your unique industrial process. With support for over +400 PLC & controller communication protocols, EBPro enables our HMIs to seamlessly integrate with your new or existing system.


Programmable Logic Controller (PLC) Connectivity
With over +400 PLC & Controller communication protocols, these HMIs will easily integrate with your preferred PLC brands, including:
- Allen-Bradley
- Siemens
- Omron
- Emerson
- GE
- Panasonic
- Mitsubishi
- …and many more
Industries Around the World
Improved traceability provides valuable data
Companies around the globe rely on Maple Systems products to help ensure uninterrupted production of critical resources. Whether you’re designing for a new application or updating an existing one, Maple Systems offers industrial automation and networking solutions that provide the connectivity, monitoring and control required to get the job done.
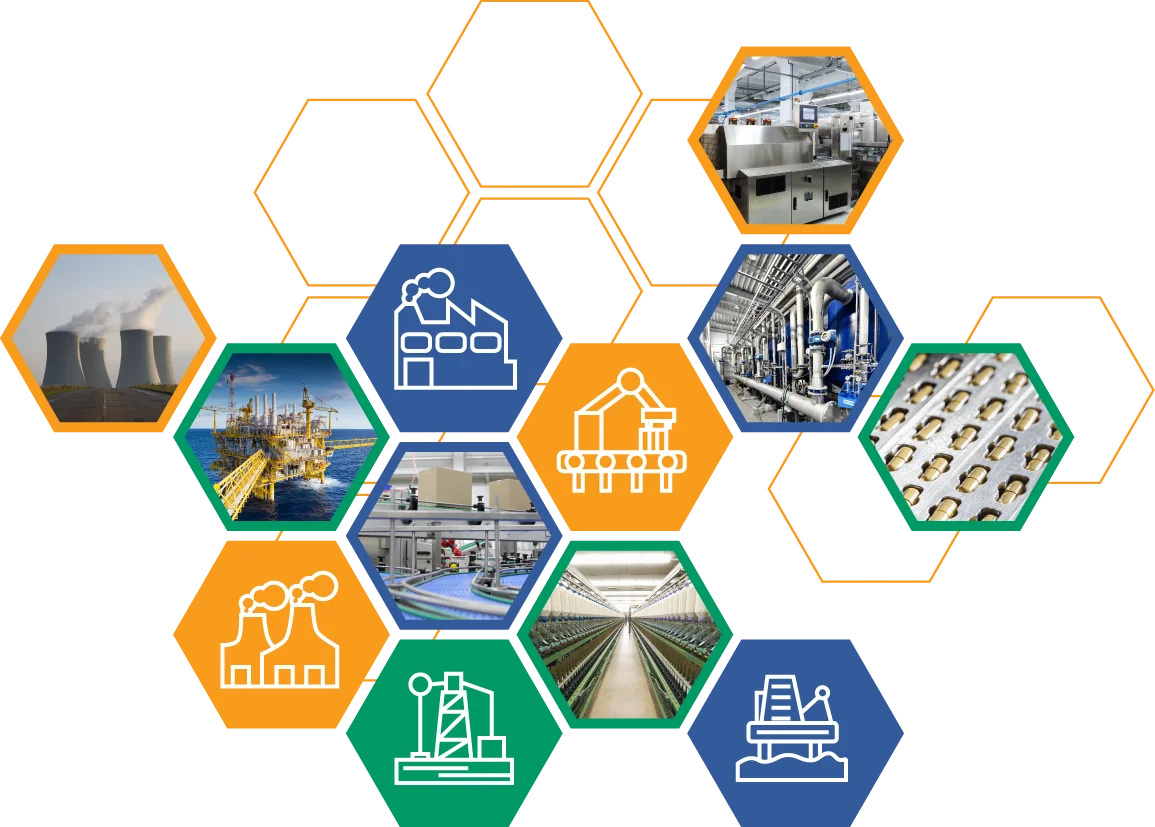

Read our Case Studies
See why our customers are so happy and continue to use our products year after year
Read Case Studies & Application Stories about how Maple Systems HMIs, OITs, PLCs, Industrial PCs, and HMI + PLCs are used in real-world applications. These case studies and success stories illustrate how our customers use our products to reduce costs and excel in building projects with Class I, Division 2 applications.
Supervisory Control and Data Acquisition (SCADA)
Early on, these types of systems were built using proprietary hardware and software, operating in isolation without connections to other networks. Operators had to reside in a centralized control room or command center because human-machine interfaces. (HMIs) did not support remote access. Any information provided to personnel other than operators was delivered via reports, which often had a significant time lag. Once devices were connected to much larger networks, they became more complex and gained broad capabilities.
To learn more about how our Class I, Division 2 products work together to create scalable SCADA solutions, visit our SCADA solutions page.
