Your cart is currently empty!
1. Compatibility
One of the first things to consider when choosing a new PLC is how well it will integrate with your existing systems. Compatibility with current hardware, software, and communication protocols is essential to ensure smooth operation. Consider whether the new PLC can communicate effectively with your existing equipment, like Human-Machine Interfaces (HMIs), Variable Frequency Drives (VFDs), and other control systems. It is also important to think about future expansions or upgrades. Choose a PLC that is scalable and can adapt to future technological advancements.
2. Hardware features
When choosing a new PLC, understanding the various hardware features is crucial. Each component plays a significant role in the overall performance and suitability of the PLC for your specific application. This section delves into the critical hardware features you need to consider: CPU (central processing unit), memory, communication interface, I/O ports, and their types (digital, analog, HSC/PWM), and the difference between expandable and fixed designs.
CPU (Central Processing Unit)
The CPU is the heart of the PLC, responsible for executing control instructions, processing data, and managing the overall operation of the system. When evaluating the CPU, consider its speed (measured in MHz or GHz), which affects how quickly it can process instructions. A faster CPU is beneficial for complex and high-speed applications. Additionally, assess the architecture of the CPU (such as 32-bit or 64-bit) as it impacts the efficiency and the amount of data it can handle at once.
Memory
PLC memory falls into two categories: program memory and data memory. Program memory stores the control program, while data memory holds the process variables. The size of the memory (often measured in KB or MB) determines the complexity of the programs the PLC can handle and the amount of data it can store. For larger systems with more complex operations, choosing a PLC with more memory is preferable.
Communication interface
The communication interface of a PLC is crucial for network connectivity and interaction with other devices. This includes Ethernet ports for network communication, serial ports using RS-232/RS-485 for device connection, and USB ports for programming and diagnostics. Evaluate the types and number of communication interfaces available to ensure they meet your system’s connectivity requirements.
I/O ports
Input/output (I/O) ports serve as the crucial connection points where a PLC interacts with the external environment. These ports gather data from sensors (inputs) and transmit control signals to actuators (outputs).
- Analog: Inputs that can read analog signals are used for sensors that provide a continuous range of values, like temperature or pressure. Analog outputs control devices that require variable signals.
- Digital: Digital inputs are for sensors with on/off states such as switches, while digital outputs control devices like relays or contactors.
- HSC (high-speed count): HSC inputs are used for applications requiring precise counting of high-speed processes as encoder signals.
- PWM (pulse width modulation): PWM outputs could be used to control the speed and position of devices like servo motors by varying pulse widths.
When selecting a PLC, it’s essential to carefully evaluate the quantity and variety of I/O ports required, ensuring they align with the specific demands of your application.
Expandable vs. fixed PLC design
- Expandable PLCs: Thanks to their modular design, expandable PLCs offer a flexible, scalable solution for a wide range of automation needs. They allow for easy integration and customization by adding or removing input/output and specialty modules, catering to specific process requirements. This adaptability makes them cost-effective and future-proof, as they can evolve with changing needs without necessitating a complete system overhaul. Additionally, their compact size and ease of maintenance make them ideal for space-constrained environments and can simplify system upgrades.
- Fixed PLCs: Fixed PLCs integrate the CPU, I/O, and communication interfaces into a single unit. They are typically more compact but offer less flexibility for future expansion or customization. Fixed PLCs are suitable for smaller systems with defined and stable requirements. The right combination of hardware components will ensure that the PLC can efficiently handle your industrial processes and adapt to future changes or expansions. Careful consideration of these aspects will lead to a more informed decision, aligning the PLC capabilities with the specific needs of your application.
3. PLC programming languages
PLCs typically support multiple programming languages, each with their own unique features and best use cases. Understanding the differences between these languages can impact the efficiency and effectiveness of your PLC programming.
Ladder logic diagram (LD)
Ladder logic diagram is the most traditional and widely used PLC programming language. It mimics electrical relay logic (on/off states) and is visually represented in a format resembling a ladder, with rungs representing control logic. Ladder logic is particularly user-friendly for those with a background in electrical engineering or relay control systems. It is best suited for simple control systems and applications where binary decisions are predominant.
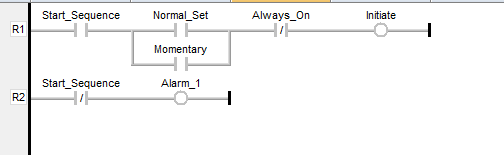
Instruction list (IL)
Instruction list is a low-level programming language like assembly language. This text-based language consists of a series of instructions, with each representing a different operation. Its compact and efficient nature makes it suitable for applications with limited memory and processing power. However, it requires a good understanding of programming concepts and is less intuitive than graphical languages like Ladder Logic.
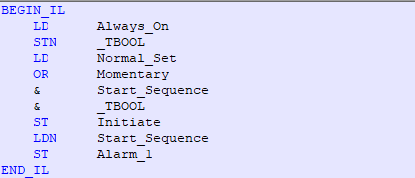
Function block diagram (FBD)
Function block diagram is a graphical language that uses blocks to represent functions, with lines connecting them to define relationships. Each block can represent a simple function like a timer or a more complex operation like a mathematical function. FBD is particularly effective for process control and applications involving complex mathematical operations. It is user-friendly for those with a background in control systems and process engineering.
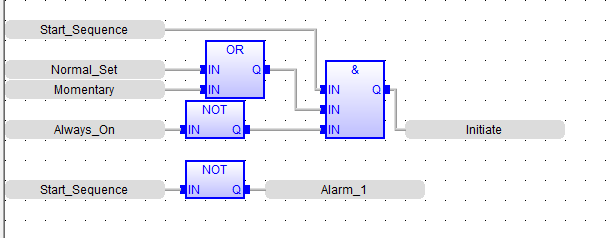
Structured text (ST)
Structured text is a high-level textual programming language that uses statements like languages like Pascal or C. It is suitable for complex applications that require algorithms, data processing, or tasks that are difficult to represent graphically. ST is best used in applications requiring complex control processes, calculations, and data manipulation.

Sequential function charts (SFC)
Sequential function charts are used to describe the sequence of control operations in a system. SFCs are graphical and represent a process flow, making them ideal for sequential control processes and tasks that require coordination of multiple operations or stages. They are especially useful in batch processing and applications where the sequence of operations is a critical aspect.

While all these programming languages offer similar functionality, your choice of programming language can significantly impact the development time, ease of maintenance, and scalability of your control systems. Selecting the right programming language depends on the specific requirements of your application, the complexity of the tasks, and the background of the personnel involved in programming and maintenance.
4. PLC software features
In addition to the hardware and programming languages, the software used to program and manage PLCs is equally crucial. Modern PLC programming software offers a range of features that can significantly enhance productivity, ease of use, and troubleshooting.
Online editing
Online editing allows programmers to modify the PLC program while it is running. This feature is invaluable for making real-time adjustments without stopping the entire process, thereby minimizing downtime. It enables immediate testing and optimization of the control logic, but it requires careful handling to avoid unintended disruptions to the operating process.
Simulation modes
Simulation modes enable testing of PLC programs without the need for physical hardware. This feature is crucial for validating logic, troubleshooting, and training purposes. It allows programmers to simulate different scenarios and conditions, identify errors, and optimize program performance before deployment.
Automatic detection
Automatic detection in PLC software aids in identifying connected devices and configuring them appropriately. This feature simplifies the setup process, especially in complex systems with multiple devices, by automatically recognizing and integrating them into the PLC environment.
Find and replace
Find and replace functionality is essential for efficient programming, particularly in large and complex programs. It allows for quick modifications across the program, saving time and reducing the potential for manual errors.
Cross referencing
Cross-referencing is a feature that helps in tracing where and how certain variables or elements are used throughout the program. This is particularly useful for debugging and understanding the flow of the program, especially when working with large or complicated PLC programs.
Custom function block libraries
Custom function block libraries allow users to create and store reusable blocks of code. This feature enhances efficiency by enabling programmers to use these predefined blocks in various parts of the program or in future projects, ensuring consistency and reducing repetitive coding efforts.
Diagnostic tools
PLC programming software may also provide users with diagnostic tools for effective troubleshooting and system maintenance. These tools actively track PLC operations through real-time monitoring and logging and can identify hardware and software issues using diagnostic utilities. They ensure reliable PLC communications through network diagnostics and promptly alert users to system irregularities. These tools play a crucial role in maintaining system reliability and performance in PLC operations.
Documentation
Comprehensive documentation within the PLC software is invaluable for programming and maintenance. It should include detailed help files, guides, and examples. Good documentation is especially helpful for training inexperienced users and for reference during complex programming tasks.
User experience
The overall user-friendliness of the PLC software cannot be overstated. An intuitive interface, easy navigation, clear labeling, and accessible help features make the software more approachable for new users and efficient for experienced programmers. User-friendliness enhances productivity and reduces the learning curve associated with new software.
The software features of a PLC play a crucial role in the efficiency and effectiveness of the entire control system. Features like online editing and simulation modes bring flexibility and safety to the programming process. Automatic detection and cross-referencing streamline setup and troubleshooting. Custom function block libraries, comprehensive error codes, and thorough documentation enhance the efficiency and ease of programming. Lastly, user-friendliness ensures that the software is accessible to users of all skill levels, making it a critical factor in the overall productivity of the PLC system. By considering these software features, users can significantly optimize the programming, operation, and maintenance of their PLCs.
5. Power
The way a PLC is powered and the voltage levels used by its I/O interfaces can significantly influence its compatibility and efficiency in various industrial applications.
Supply voltage
PLCs are designed to operate on specific supply voltages, and it is crucial to ensure compatibility with your facility’s power supply. Commonly, PLCs operate on:
- 24/48V DC: This is the most prevalent voltage for PLC systems, especially in industrial environments. 24V DC is preferred due to its safety and reliability. It is low enough to be safe for operators and sensitive equipment, yet sufficient to ensure reliable signal transmission.
- 120V: Some PLCs are designed to operate on standard AC voltage levels. These are most often used for large-scale control circuits and may be more cost-effective by reducing the need for multiple separate power supplies.
I/O voltage
The voltage levels used by the PLC’s Input/Output (I/O) interface are crucial since they must be compatible with the sensors, actuators, and other devices connected to the PLC. Common I/O voltage levels include:
- DC Voltage Levels: For digital inputs and outputs, common levels are 5V DC, 12V DC, and 24V DC. The choice depends on the devices connected to the PLC. For example, 24V DC is widely used in industrial applications due to its robustness and noise immunity.
- AC Voltage Levels: AC inputs and outputs might also operate at 120V AC. This is typically used for applications involving higher power devices such as motors or large heating elements and can reduce costs by centralizing the power supply for multiple devices in one place.
Selecting the appropriate power supply and voltage levels for a PLC is vital for ensuring reliable operation and minimizing the risk of equipment damage or operational inefficiencies in different industrial environments.
6. PLC scan time
Understanding the concept of scan time is critical when selecting a PLC for any industrial application. Scan time directly affects the perceived processing speed of a PLC and plays a pivotal role in the controller’s ability to meet the demands of dynamic and time-sensitive processes.
Scan time and processing speed
The scan time of a PLC refers to the time it takes to complete one cycle of its operational process, which includes reading inputs, executing the control program, and updating outputs. This cycle is continuous and typically measured in milliseconds (MS). The faster the scan time, the more responsive the PLC is to changes in input conditions, making it crucial for applications requiring real-time control and rapid decision-making.
A shorter scan time means the PLC can process data and react to inputs more quickly, which is perceived as a higher processing speed. This is particularly important in high-speed manufacturing processes, precise control applications, and situations where rapid response to input changes is critical.
Factors contributing to increased scan time
Several factors can contribute to increased scan time in a PLC, potentially affecting its performance in time-sensitive applications:
- Control program complexity. More complex programs with numerous instructions, intricate logic, or extensive mathematical calculations can increase scan time. Each additional operation requires processing time, thus extending the overall cycle time.
- I/O processing. The number of input/output points and the type of processing (analog vs. digital) can impact scan time. For example, analog signal processing generally takes longer than digital due to the need for signal conversion and scaling.
- Data logging and reporting features. Advanced data logging and reporting can increase scan time, particularly if the PLC is processing and storing large amounts of data or generating complex reports.
- Specialized functions and modules. Special functions like PID control, high-speed counters, or specialized modules (such as motion control) can lengthen the scan time, as these tasks are typically more processor intensive.
- Processor speed. Processor speed is a critical aspect of PLC performance, particularly in environments requiring rapid response times and high-speed data processing. The speed of the PLC’s processor determines how quickly it can execute the control program and manage tasks like I/O processing and communication.
Optimizing scan time
To optimize the scan time, it is essential to balance the complexity of the control program with the PLC’s processing capabilities. Simplifying control logic where possible, optimizing data handling, and ensuring efficient communication can help reduce scan time. Additionally, selecting a PLC with a faster processor and more memory can alleviate the effects of increased scan time due to complex operations or extensive I/O processing.
By considering the complexity of the control program, the nature and quantity of I/O processing, communication needs, and special functions, you can choose a PLC that provides the optimal balance between functionality and responsive performance.
7. Environment
Environmental factors like temperature, vibration, humidity, dust, and corrosive atmospheres can significantly impact the performance and longevity of a PLC. Understanding how these factors affect PLCs is crucial in choosing a model that can withstand specific environmental challenges.
Operating temperature
Temperature is one of the most critical environmental factors affecting PLCs. Each PLC is designed to operate within a specified temperature range, usually provided in its technical specifications.
- High Temperatures: Excessive heat can lead to malfunction or damage to the electronic components of a PLC. High-temperature environments often require PLCs with enhanced cooling systems or those designed with heat-resistant materials.
- Low Temperatures: Similarly, extremely low temperatures can affect the performance and reliability of a PLC. In such conditions, PLCs with special provisions to combat cold, like built-in heaters or insulation, are necessary.
Vibration
Vibration is another significant environmental factor, especially in industrial settings with heavy machinery. Constant vibration can cause mechanical wear, loosening of connections, and potential failure of electronic components. Choose PLCs designed to withstand the level of vibration typical in your operational environment. These PLCs often have ruggedized components and reinforced mounting systems to endure continuous vibration without degradation of performance.
Humidity
High humidity can lead to condensation and corrosion in electronic circuits. PLCs operating in humid environments should have adequate protection against moisture.
Dust and corrosive atmospheres
In environments with elevated levels of dust or corrosive substances, PLCs with higher ingress protection ratings are necessary. These PLCs are designed to prevent the ingress of dust and resist corrosive materials.
Electromagnetic interference
PLCs should have proper shielding and grounding to prevent operational disruptions in areas with high levels of EMI, such as near heavy electrical equipment or radio transmitters.
Explosive atmospheres
In industries where explosive gases, vapors, or dust are present, it is vital to select PLCs certified for use in such hazardous environments. These PLCs feature designs that actively prevent the ignition of the surrounding atmosphere. They typically have seals to block the ingress of explosive substances and are constructed to minimize the risk of generating sparks or excessive heat.
A thorough evaluation of the operating environment in terms of temperature, vibration, humidity, dust, and other factors is essential to ensure the chosen PLC can operate reliably under those conditions. By considering these environmental factors, you can significantly reduce maintenance issues and prolong the lifespan of the PLC.
8. Certifications
It is important to consider various certifications that indicate compliance with safety, quality, and environmental standards for a new PLC. These certifications serve as benchmarks for reliability and performance in different environments and applications. Understanding what each certification represents can help in choosing a PLC that meets specific regulatory and operational requirements.
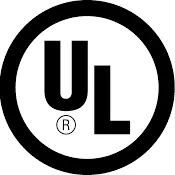
UL (Underwriters Laboratories)
UL certification signifies that the PLC meets stringent safety standards, primarily for the North American market. This certification indicates that experts have tested the PLC to ensure it complies with safety-related requirements, including risks like fire, electric shock, and related hazards.
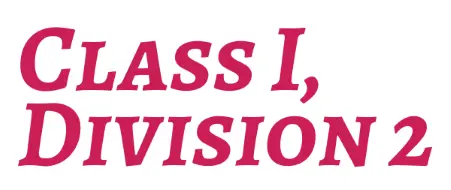
Class I, Div 2
The UL organization issues this certification specifically for devices used in hazardous locations. Class I, Div 2 certified PLCs are designed to operate safely in environments where flammable gases or vapors may be present under abnormal conditions.
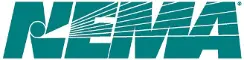
NEMA (National Electrical Manufacturers Association)
NEMA ratings define the types of environments in which an electrical enclosure can be used. A PLC with a NEMA rating is certified for protection against factors like dust, water, and corrosion, making it suitable for various industrial conditions.
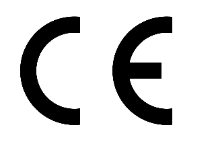
CE (Conformité Européenne)
The CE mark indicates that the PLC complies with the necessary European Union regulatory requirements, particularly in terms of health, safety, and environmental protection. It is mandatory for products sold within the European Economic Area.
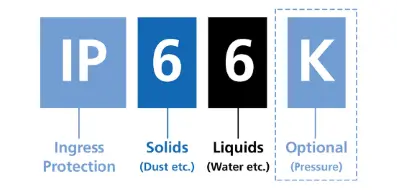
IP (Ingress Protection)
IP ratings, denoted as IP followed by two digits, indicate the level of protection a PLC offers against solids and liquids. The first digit represents protection against solid objects, and the second digit represents protection against liquids. Higher numbers mean better protection.
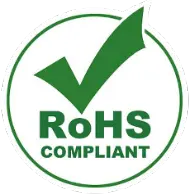
RoHS (Restriction of Hazardous Substances)
RoHS compliance means that the PLC does not contain specific hazardous materials banned by the European Union, such as lead, mercury, and cadmium. This certification is important for environmental protection and health safety.
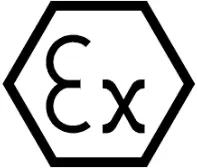
ATEX (Atmosphères Explosibles)
ATEX certification applies to equipment intended for use in explosive atmospheres in the European Union. It ensures that the PLC is designed to prevent ignition and can safely operate in potentially explosive environments.

FCC (Federal Communications Commission)
The FCC certification is relevant in the United States and indicates that the electromagnetic interference from the PLC is under limits approved by the Federal Communications Commission. This is important for preventing undue interference with other electronic devices.
These certifications ensure that a PLC is suitable and safe for specific applications and environments. This not only ensures compliance with legal standards but also guarantees that the PLC will perform reliably and safely under the designated conditions.
9. Size
The physical size of a PLC is an often overlooked but crucial factor in the selection process. The size of a PLC can have a significant impact on its installation, integration, and usability in various industrial settings.
Space constraints
In many industrial environments, space can be a premium commodity. Facilities with limited space in control cabinets or on manufacturing floors require compact PLCs that can fit into small areas without compromising functionality. A smaller PLC can be advantageous in such settings, allowing for efficient use of space.
Scalability and expansion
The size of a PLC can also influence its scalability and ability to expand. Modular PLCs, which allow for the addition of extra modules such as I/O, communication, or special functions, tend to occupy more space as they expand. Understanding the physical space available and future expansion needs is crucial in selecting a PLC of appropriate size.
Heat dissipation
PLC size can also affect its heat dissipation capabilities. Larger PLCs have more surface area, which can aid in better heat dissipation, whereas compact PLCs might require additional cooling mechanisms, especially when installed in confined spaces or in environments with high ambient temperatures.
Installation and maintenance
Larger PLCs might offer easier access for installation, wiring, and maintenance, as there is typically more room to work around the unit. However, compact PLCs, while space-efficient, may present challenges in terms of accessibility for maintenance and modifications.
When choosing a new PLC, consider the available space, the potential need for expansion, heat management requirements, and ease of installation and maintenance. A well-chosen PLC in terms of size can lead to smoother integration, better use of space, and overall operational efficiency in your industrial processes.
10. Support resources
In the world of industrial automation, choosing the right PLC involves more than just technical specifications; the availability and quality of support resources play a pivotal role in the PLC’s long-term performance and user satisfaction.
Documentation
Comprehensive and accessible documentation is the first line of support for any PLC. Detailed manuals, installation guides, and troubleshooting resources are indispensable for both initial setup and ongoing maintenance. These resources should be clear, thorough, and tailored to various skill levels, ensuring that users can effectively operate and maintain the PLC, regardless of their level of expertise.
Training and education
Given the complexity and evolving nature of PLC technology, robust training programs are essential. Manufacturers should offer guidance covering operational nuances, programming techniques, and best practices whenever possible. This training can be delivered through various formats, including online videos, webinars, and tutorials, facilitating continuous learning and skill development for users.
Technical support
Reliable customer support is a cornerstone for troubleshooting and resolving issues swiftly. Manufacturers should provide multiple channels of support, such as phone, email, and chat services, staffed by knowledgeable technicians. The availability of quick and efficient technical assistance minimizes downtime and ensures smooth operations, which is crucial in time-sensitive industrial environments.
Having a robust library of documentation, tutorials, and demo projects can significantly reduce programming and installation costs, and a responsive customer support team can be invaluable when unexpected challenges arise.
Conclusion
Choosing a new PLC for your industrial application is a multifaceted decision that hinges on a deep understanding of both your current requirements and future aspirations. It involves a careful assessment of compatibility with existing systems, the intricacies of hardware features like CPU, memory, and I/O ports, and the suitability of various PLC programming languages.
Additionally, the software features play a pivotal role in enhancing productivity, ease of use, and troubleshooting capabilities. As industries continue to evolve and integrate more sophisticated technologies, the choice of a PLC becomes increasingly critical. It’s not just about meeting today’s needs but also about ensuring scalability and adaptability for tomorrow’s challenges.
Contact us
Would you like to know more? Our friendly and knowledgeable sales team can connect you to the resources you need. For information on pricing, availability, and more, send an email message to sales@maplesystems.com, or contact our team by phone at (425) 745-3229.
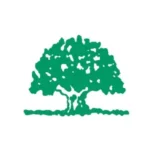
About the Author