Your cart is currently empty!
1. Driver support
Perhaps the most important function an HMI has is the ability to connect to and communicate with other devices. When devices are connecting, they need a set of instructions to know how to communicate with each other. These instructions are commonly known as drivers. A driver is a critical software component that provides an operating system with the information it needs to send or receive data between itself and another device. Some devices require drivers that are specific to a particular model, while others may use drivers for a generic protocol, like Modbus.

Before buying new HMI hardware, confirm with the manufacturer that driver support is available for all the devices that the HMI would need to communicate with. Some manufacturers provide driver support solely for their own devices, so if maximizing flexibility is a priority, it may be advantageous to find a manufacturer who provides driver support for third-party devices as well. For more information about specific device drivers, visit our Controller Information Sheets page to see a listing of some of the most commonly used drivers in industrial controls.
2. Communication ports
To establish communication between an HMI and other system components, the HMI must have the appropriate communication ports for connecting to devices like PLCs, printers, modems, cameras, and various other components. The most common ports for industrial controls include Serial, Ethernet, and USB, but the suitability of a device for a specific project often depends on the combination of available ports.
Serial
Despite the rise and adoption of Ethernet, serial communication has historically been the dominant means of communication for industrial control systems. Consequently, manufacturers still commonly include serial ports in new HMI hardware, and HMIs support two primary types of serial protocols: RS-232 and RS-485.
RS-232 (2w/4w)
RS-232 is a standard serial protocol that uses a 9-pin or 25-pin connector. Created in 1962, the RS-232 protocol still sees widespread use for connecting HMI devices to various industrial components, such as PLCs or other control systems.
The RS-232 protocol does have limitations as compared to more recent protocols, including a short transmission distance of 50 feet or less before signal degradation can become a concern, and a relatively slow transmission rate compared to more modern options such as Ethernet. RS-232 is also point-to-point only, meaning that it can only be used to connect between two devices.

RS-485 (2w/4w)
In 1998, the approval of the RS-485 protocol addressed the shortcomings of its predecessor, RS-232, allowing for more stable, noise-resistant communication over longer distances. RS-485 commonly uses a 9-pin serial port to connect to an HMI.
RS-485 also introduced the ability to communicate with multiple devices over the same bus, sometimes referred to as “multi-drop” communication. This allows an RS-485 network to connect up to 32 devices, or many more than that if repeaters are present to extend the network.

USB
The Universal Serial Bus (USB) is a standard interface that is used to connect peripheral devices to a host controller such as an HMI. Widely used in all kinds of devices since its launch in 1996, there are multiple versions of the USB standard, each with their own port configurations.

USB ports enable an HMI to connect to various devices, including input devices like keyboards or mice when touch input is not in use. These ports can also expand an HMI’s storage capabilities by connecting to external storage devices such as USB flash drives, allowing for the storage and transfer of program data, historical logs, and media files.
Ethernet
Ethernet is the most popular networking technology in use today and offers a reliable, relatively inexpensive method of networking devices together. An RJ-45 connector is typically used for Ethernet connections, and modern HMIs often include at least one Ethernet port for wired connections.
There are several advantages that Ethernet provides when compared to serial protocols. Serial ports often have unique pin configurations that require specialized cables to connect, while Ethernet ports are far more standardized with fewer variations of cables to choose from. Ethernet is also capable of higher data transfer rates, with speeds up to 400Gbps at the high end.

It is often necessary to connect an HMI to devices on a local network as well as a wide-area network to facilitate communication. Modern HMIs may include two or more Ethernet ports for this purpose, which would allow the device to communicate with local devices while having direct access to the internet at the same time.
Wi-Fi
Wireless ethernet communication has multiple advantages as compared to a traditional wired network. Wireless networks require fewer cables, allow for mobile devices to communicate with the network, and data can be transmitted across relatively large areas from a single access point. At the same time, there are aspects of wireless communication that may make it a poor choice for certain situations.
Since data broadcasts use a radio signal, signal quality issues may arise that affect network performance, and unauthorized parties could potentially intercept the wirelessly sent data. For situations where connection speed and security are paramount, a wired connection may be the better option.
3. Display properties
Size
Space, visibility, ergonomics, and user experience are some of the factors that may influence what size of HMI is right for a given application.
Larger screens provide programmers with more real estate, allowing them to space objects comfortably apart and view displays with trend data clearly, even when charting many data points simultaneously. Smaller screens may be more appropriate for situations where space is at a premium, or if there is a need to install the unit into a pre-determined cut-out or within some other constrained space.

If an HMI is to be installed in an enclosure or existing cutout, take careful measurements to ensure that the unit will fit in the space available. Most HMIs have a lip around the unit that can rest on the edge of a cutout, so make sure that the cutout is big enough to allow the back of the HMI to fit inside, but small enough that the lip of the unit will rest on the surface.
Resolution
Display resolution is a measurement of the number of pixels present on a screen and is a major component of the overall picture quality that a screen can display. In general, screens with higher resolutions display images with finer detail and clarity compared to lower resolution counterparts, making them well-suited for larger screens.

That being said, not all applications require high resolution output. If a project requires an HMI to display only a few simple objects and some text labels, a lower resolution display may suffice. Evaluating the project’s scope and determining the HMI’s specific use is essential before deciding on the required resolution. If unsure, it may be better to err on the side of higher resolution, as this will allow for future growth.
When designing a program for an HMI, designers generally lay it out and optimize it for a specific resolution. Changing the program’s resolution affects the object sizes and spacing between them, likely requiring reformatting of the program. When buying an HMI with the intent to install an existing program onto it, finding one that supports the project’s target resolution can save a considerable amount of time spent resizing and placing every object.
Brightness
When an HMI is in a location with glare or high ambient light levels that could hinder an operator’s ability to identify screen objects, having an screen capable of displaying at high brightness may be essential for the operator to perform their tasks and monitor values on the screen.
Screen brightness can be measured in units called nits. A typical screen may have an output anywhere between 200-600 nits, while units capable of displaying above 1000 nits are classified as high-brightness.
4. HMI programming software
Creating a program that includes all the necessary elements that a project requires can be time-consuming, so having a programming environment that is intuitive, powerful, and flexible can be the key to unlocking an HMI’s potential. When shopping for new hardware, take some time to review the software that comes with it to make sure that it provides all the functions required for a project to succeed.
Alarms and event monitoring
Being able to monitor values and receive automated alerts when an unexpected event occurs is a critical feature for modern HMI devices. When something goes wrong, having a system that can detect the issue quickly and notify the appropriate parties can prevent disaster, and is a must for many operations.
Data logging
An essential feature of many control systems, data logging functionality gives an HMI the ability to store incoming data in memory and then use that data to create historical records and display trend data. When this functionality is required, selecting an HMI that has data sampling features and adequate storage for logged data is an important step.
Database integration
Database programs such as SQL are frequently used by businesses to compile and organize large amounts of data for a variety of purposes. When performed manually, the process of maintaining a database can be a slow and tedious process. If this is a concern, look for an HMI that can connect to a database directly so that manual data entry is not required.
Email notifications
Operational alerts, warnings, maintenance reminders, and performance reports are a few of the common types of notifications that an administrator may need to monitor the status of their control systems and ensure that a production line is operating safely. Email notifications play a vital role in facilitating quick and timely actions in an industrial environment, contributing to safety, efficiency, regulatory compliance. Having a well-configured email notification system in place to ensure the right people get the right information at the right time can be crucial to the success of an operation.
Recipes and formulas
Some processes may require saving a set of parameters for easy and accurate repetition during production.. Recipes can store material data, temperature, pressure, size, and a wide array of other parameters. Recipes enhance efficiency by eliminating the need for manual entry of parameters every time a process runs, thereby increasing the overall consistency and quality of a product.
Programming experience
Having an intuitive interface with simple controls and user-friendly features can make a tremendous difference when it comes to deploying projects quickly and efficiently. How easy the development software is to use largely depends upon the experience of the programmer using it, but there are other factors that may influence how easy a particular piece of software is to use. There is often an inverse relationship between ease-of-use and functionality when it comes to programming software.
Programming software that offers maximum flexibility and granular control over all aspects of a system can often present a challenge to designers, as it may require adjusting dozens of parameters to achieve a certain result. On the other hand, software that is easier to use often achieves this by simplifying their controls and removing certain functions, thereby reducing its potential. It is important to select an HMI that uses programming software that matches the skill level of the developer while providing all the necessary controls and features for a given application.
Support resources
If unfamiliar with the programming software used with an HMI, review the support resources available for it to ensure that the developers have provided adequate documentation and instructional materials for their software. Learning how to use new software without the aid of a well-structured support library can be a frustrating experience that requires a tremendous amount of time and research. Having access to support technicians, demonstration programs, tutorials, and thorough documentation can make all the difference when trying to understand the ins and outs of a new programming environment. Some manufacturers provide free software and support resources to their customers, but not all, so it is best to research these aspects of the total cost so there are no surprises further down the road.
5. Performance
Several factors determine the speed at which an HMI processes data, but the Central Processing Unit’s (CPU) clock speed and the amount of Random Access Memory (RAM) are generally the greatest contributors to overall system performance.
CPU
The CPU is essentially the brain of any computing device and is responsible for interpreting and carrying out instructions from software and connected hardware devices. The clock speed of a CPU, measured in hertz, represents the number of instructions a processor can execute per second. For instance, a 1 GHz processor can execute up to 1 billion cycles per second under ideal conditions.

Modern HMIs commonly use a few types of CPU architectures, including ARM, x86, and RISC-V:
- ARM CPUs are widely used due to their power efficiency and versatility. They’re commonly found in lower power devices and are often used in portable or battery-operated HMIs. Many HMI systems use the Cortex series of ARM processors, such as the Cortex-A and Cortex-M series. The ARM architecture supports a wide range of software, including real-time operating systems, Linux, and Android.
- X86 CPUs, typically more powerful than ARM CPUs, power HMI systems that demand higher processing power or run complex applications. Manufacturers frequently use them in industrial control systems, medical equipment, and aviation systems.
- RISC-V is an open standard architecture based on established reduced instruction set computer (RISC) principles. As an open standard, RISC-V is used in various specialized systems, and can be adapted for use with a wide range of custom applications.
RAM
Working in tandem with the CPU, the system’s RAM provides a memory space that the processor can use to temporarily store data it needs to perform an operation on. When the CPU needs to process data that resides in stored memory, it will place the necessary data into RAM, perform the required operations, then clear the RAM so it can hold the next data set.

Depending on the amount of data that needs to be processed, the system may need to fill the RAM with data multiple times before it can complete the entire process. The process of moving data into RAM and then out again takes time, so having a large amount of RAM space available can have a positive effect on performance, as it will reduce the number of transfers required to complete a given operation.
Other factors
However, the overall performance of an HMI is not solely based on its CPU speed and RAM capacity. Other elements can influence the speed at which a device can process data. Complex projects with many variables, numerous screens, or intricate graphics will typically require more powerful processing capabilities.
Device communication also plays a role in the system’s performance – the speed at which an HMI can interact with other devices and exchange information can have a substantial impact on its perceived processing speed. Data logging and transfers can also play a role, as these processes consume a significant amount of system resources. Furthermore, custom functions such as specialized algorithms or macros can add to the processing load, potentially slowing down the system. For these reasons it is a good idea to evaluate the entire scope of a project and then choose an HMI with enough processing power to handle necessary operations without crashing or creating system lag.
6. Remote access
A single administrator often manages systems at multiple locations, and having to travel to each site for routine tasks can be time-consuming and expensive. Having the ability to monitor and control devices remotely from a single location can greatly increase efficiency and allow for immediate access when an urgent need arises. Having remote access can also allow administrators to install program updates, gain access to devices connected to an HMI by using passthrough features, and transfer logged data all from a central location. To facilitate this kind of oversight, remote access support is becoming an increasingly common feature included with modern HMI devices.

Once you establish a connection to a remote device, client software installed on a PC or mobile device enables a user to interact with the remote HMI’s operating system as if they were in front of the panel itself. The specific software used for this purpose may vary, but many manufacturers support Virtual Network Computing (VNC), a commonly used remote sharing system. Some companies may offer their own proprietary solutions for remote access, such as cMT Viewer or FactoryTalk, for example. Reviewing the available options for remote access and deciding what solution best fits a project’s needs is a key step, as each option may require specific hardware or software to implement properly.
Client-only devices such as Web HMIs are well-suited for many remote access applications, as they are designed to work in concert with a central server and do not require extensive configuration to do so.
7. Security
Designing and maintaining security for a system can require extensive planning, and securing an HMI is a significant piece of the puzzle when it comes to protecting sensitive data. Whether it is a matter of preventing intrusion from unauthorized users, protecting valuable intellectual property, or ensuring that operators cannot access potentially dangerous controls without the appropriate credentials, creating an air-tight security plan for any system can be a complex process. Because of this, it is critical that an HMI has security features that are flexible enough to be applied to a wide range of possible use cases.
User accounts
When multiple operators are regularly working with a single HMI terminal, it may be necessary to restrict access to screens or functions that should only be available to specific users. Allowing every operator to have full control over functions and system settings can be dangerous if those individuals are not properly trained.
To address these risks, many HMIs have tools that allow a designer to create user classes with associated access levels that will prevent users from interacting with portions of the project that they should not have access to. Creating user accounts with different access levels can allow a designer to create and install a single program on an HMI that includes all the necessary information and control that any user might require, while preventing access to sensitive data and controls.
Protecting IP
For integrators and control systems engineers who program, deploy, and support projects for clients, having tools to restrict access to their work and protect their intellectual property can be crucial to the success of their business. Modern HMI devices and software can include features such as prohibiting access to the source program installed on a device, or adding password locks that prevent the end-user from editing or reverse engineering someone else’s work.
Encryption
In situations where an HMI needs to connect to the internet for communication, ensuring the secure transmission and receipt of sensitive information is critically important. If a project requires sending emails from the HMI, you should review the device’s specifications to check the supported versions of TLS or SSL encryption. Also, if the HMI’s operating system supports remote access features, verify that it encrypts the connections established for this purpose.
8. Certification
Challenging environmental conditions and safety regulations may require that a device is certified by a trusted organization to ensure that it is safe to use when exposed to adverse conditions. When installing devices in facilities with high humidity, liquids, dust, or other hazardous materials that can damage sensitive electronics and jeopardize safety and productivity, it is extremely important to ensure the HMI has certification to operate in those conditions.

UL
Underwriters Laboratories (UL) is an independent science and safety organization that evaluates and certifies products, processes, and materials to ensure that they meet industry standards for safety and reliability. UL stands as one of the world’s most trusted organizations for safety and reliability testing, and many areas often require their certification.

Class I, Div 2
The UL organization issues this certification specifically for devices used in hazardous locations. Class I, Div 2 certified devices are designed to operate safely in environments where flammable gases or vapors may be present under abnormal conditions.

NEMA
The National Electrical Manufacturers Association (NEMA) uses a standard rating system to assess electronic devices and determine whether the enclosure used for a device is capable of resisting ingress from water or other potentially damaging materials.

CE
Conformite Europeenne (CE) is a European standard that assesses products to certify that they meet safety, health and environmental protection requirements and is a requirement for devices being sold in much of the European Union.

RoHS
The European Union adopted the Reduction of Hazardous Substances (RoHS) initiative to reduce the harmful effects of dangerous substances on people and the environment. RoHS certification indicates that a product does not contain unsafe levels of chemicals deemed hazardous. This includes testing for heavy metals such as cadmium, lead, and mercury, and other potentially dangerous elements.

Ingress Protection (IP)
Developed by the International Electrotechnical Commission (IEC), the Ingress Protection rating system measures how well the housing of a device can prevent dust, moisture, and liquids from entering the housing and damaging the components inside. The IP rating system is defined in international standard IEC 60529, and ratings will consist of two numbers. The first number indicates how well the housing protects against solid foreign objects such as dust, and the second number indicates its resistance to ingress from water. For example, IP69 is the greatest possible rating for this standard, and devices with this rating have been found to be dust-tight and protected against high pressure and temperature water jets.

ATEX
The ATEX directive, a certification system developed for use in the EU, assesses whether a device can be used safely in environments with explosive materials. Within the EU, all devices used in hazardous or explosive atmospheres require ATEX certification.

FCC
The Federal Communications Commission certification confirms that a device’s electromagnetic radiation falls within established limits and should not interfere with other electronic devices’ operation in the surrounding area. Any device capable of operating in the radio frequency range of 9 kHz to 3,000 GHz requires FCC certification.
9. IIoT support
OPC/UA
OPC Unified Architecture is a machine-to-machine communication protocol that is platform independent and uses a publisher/subscriber model to communicate between devices. This protocol is a popular form of communication for industrial controls but is being adopted across many other industries as well. Given its popularity in SCADA systems, having an HMI that includes support for OPC/UA may be a good idea for businesses that need to send complex instructions between devices.

MQTT
Similar to OPC/UA, MQTT is another protocol that employs the publisher/subscriber model to send information between devices. It is known for using less bandwidth than OPC and is a good option in situations where network reliability or latency is a concern.

10. Input method
Depending on workflow or other conditions at a site, the method used to detect input on an HMI screen may be worth consideration. There are two types of touch input detection that are commonly used in modern HMIs, resistive and capacitive touch, each with their own strengths and weaknesses.
Resistive
Resistive touch input was the first widely adopted form of touch detection for devices such as HMIs. This input method is a pressure sensitive system that consists of two transparent layers of electrode film overlaid on top of each other with a gap between them. When an operator presses down on the screen, the compression of the soft top layer of electrodes contacts the bottom layer, allowing the HMI to detect the location of that point. Screens using resistive touch technology typically cost less than capacitive screens and enable operators to interact with the HMI while wearing gloves or using an object like a stylus to touch points on the screen.
Capacitive
Unlike resistive touchscreens, capacitive input does not require pressure to activate. Instead, the screen will detect input when it contacts a conductive surface such as bare skin. When the user touches a point, the screen will detect a change of capacitance at that location and register it as input. While capacitive screens are typically more accurate and responsive than a resistive screen, they can be more expensive, and the user must touch the screen with a conductive surface, which may not be practical for some work environments.
Projected capacitive (PCAP)
Commonly used in modern mobile devices such as phones and tablets, projected capacitive screens use a similar approach to detect input as regular capacitive screens do, but with some critical differences. PCAP screens will still read changes in capacitance to detect touch input, but they are more sensitive, have greater display clarity, and can detect multiple points of input at once, allowing for multi-touch control.
Compared to standard capacitive touch, PCAP screens are generally better at detecting touches when the operator is wearing gloves, though thicker gloves may prevent the screen from detecting input. If there is a need to use a stylus, be aware that it will need to have a conductive material on the tip for a PCAP screen to be able to detect it.
Contact us
Would you like to know more? Our friendly and knowledgeable sales team can connect you to the resources you need. For information on pricing, availability, and more, send an email message to sales@maplesystems.com, or contact our team by phone at (425) 745-3229.
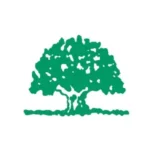
About the Author