Your cart is currently empty!
Introduction
Web HMIs provide a streamlined interface solution that makes configuring and installing your next panel easier and more secure than ever. Using a client-only Web HMI can significantly reduce compatibility and software considerations, but there are some important elements to keep in mind when comparing models. The following list breaks down nine important factors that can help you determine which Web HMI is right for you.
1. Web browser
Unlike traditional HMIs that run programs locally, Web HMIs are client-only devices that rely on a web browser to access content from a server. A web browser is an application that allows users to view and interact with HTML-based content sent over a network connection. Chromium and Firefox-based browsers are the two most commonly used browsers found on devices today.
While evaluating a new panel, pay attention to the browser’s release version, as newer versions can support the latest HTML5 web standard, allowing access to advanced content. Older browser versions may not be compatible with modern websites or could potentially expose the system to malicious attacks. Additionally, the frequency of updates is a key factor. Browsers that are regularly updated can provide better performance and improved security over time.
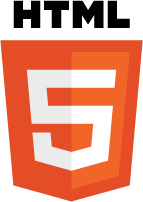
Consider the compatibility of the browser with the applications you plan to use. Some web applications, especially those that require specific plugins or JavaScript applications may only function properly in certain browsers. Analyzing your applications for any specific requirements and ensuring the browser supports them is recommended, as it can save time and prevent headaches during installation.
2. Operating system
Another important factor to consider is the operating system (OS) that powers the Web HMI, as this will heavily influence user experience, security, and system performance. Below are the most common operating systems found on Web HMIs.
Linux
Linux is an open-source OS renowned for its stability, security, and customizability, making it a favorite in industrial settings. It’s perfect for demanding environments, offering excellent control over system resources for experienced users. Among the various Linux versions, Linux Yocto stands out for thin-client devices like Web HMIs due to its flexible platform that supports scalable custom operating systems.
Windows Embedded
Windows Embedded is a streamlined version of Windows OS designed for embedded devices. Its familiar interface reduces training time and simplifies integration with existing systems. Supporting a wide range of Windows-compatible software, Windows Embedded offers flexibility but is more susceptible to viruses and requires frequent updates compared to Linux.
3. Display
Display properties such as size and resolution can significantly influence usability and efficiency. Choosing the appropriate size and resolution ensures maximum functionality and user satisfaction.
Size
Space, visibility, ergonomics, and user experience all play a critical role in determining the ideal size for a Web HMI. Larger screens can display more complex data and are easier to read from a distance, while also offering increased spacing between controls to minimize unintended interactions. On the other hand, smaller screens are more suitable for tight spaces or when display requirements are minimal.
When fitting a Web HMI into a pre-existing enclosure, precise measurements are necessary to confirm that the panel will fit into the designated space. It is also important to ensure there is enough clearance around the device to allow proper ventilation. For example, Maple Systems Web HMIs recommend having a clearance of 2 inches around the device to facilitate adequate airflow, though this may differ between device manufacturers.
Resolution
Screen resolution refers to the total number of pixels displayed on a screen, determining the image quality it can produce. Resolution is usually denoted as width times height in pixels, i.e., 1024 x 600. Higher resolution screens can show sharper images with more detail, making them particularly beneficial for larger displays.
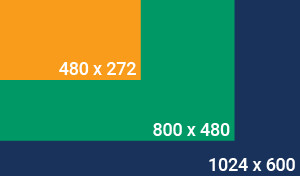
However, high resolution output may not be necessary in every case. For instance, a screen that only needs to display a few basic visual elements with text can function well at a lower resolution. When in doubt, opting for a higher resolution may be best practice to accommodate potential needs in the future.
Brightness
In brightly lit environments, high-brightness screens are essential. They ensure the display remains visible and clear under intense light conditions, which is crucial for maintaining operational efficiency and safety. Screen brightness is often measured in units known as “nits.” A typical consumer-grade screen may have an output anywhere between 200-600 nits, while units capable of displaying above 1000 nits are classified as high-brightness.
When installing a Web HMI in a location with glare or high ambient light levels that could hinder an operator’s ability to identify screen objects, having a screen capable of displaying at high brightness levels may be essential for the operator to perform their tasks. Increased brightness also allows for viewing the display from greater distances than would be possible with a standard screen.
Keep in mind that displays capable of high-brightness output generate more heat and consume more energy than standard screens. Make sure to install the unit in a location where heat can dissipate quickly without affecting other devices.
4. Performance
Generally speaking, a Web HMI does not need a large amount of processing power to perform it’s job, as data processing is handled primarily by the server. However, it is still important to make sure that the Web HMI you choose can quickly and reliably access content from the server.
For example, loading a page that has several high-resolution images will require more processing power than one that contains only basic text, leading to prolonged page loading. When assessing a Web HMI’s performance, check the hardware specs to make sure that the CPU clock speed and RAM capacity are sufficient to handle the tasks the device will be expected to perform.
5. Input method
Depending on workflow or other conditions at a site, the method used to detect input on a Web HMI screen may be worth consideration. There are three common types of touch input detection: resistive, capacitive, and projected capacitive, each with their own strengths and weaknesses.
Resistive touch
Resistive touch input was the first widely adopted form of touch detection for industrial controls. This input method is a pressure sensitive system that consists of two transparent layers of electrode film overlaid on top of each other with a gap between them. When an operator presses down on the screen, the soft top layer of electrodes contacts the bottom layer, allowing the device to detect the location of that point. Screens using resistive touch technology typically cost less than capacitive screens and enable operators to interact with screen objects while wearing gloves or using a stylus.
Capacitive touch
Unlike resistive touch, capacitive touch input does not require pressure to activate. Instead, the screen will detect input when it contacts a conductive surface such as bare skin. When the user touches a point, the screen will detect a change of capacitance at that location and register it as input. While capacitive screens are typically more accurate and responsive than a resistive screen, they can be more expensive and the user must touch the screen with a conductive object, which may not be practical for some work environments.
Projected capacitive (PCAP)
Compared to standard capacitive screens, projected capacitive (PCAP) models use the same approach to detect input, but with some critical differences. PCAP screens also read changes in capacitance to detect touch input, but they are more sensitive, have greater display clarity, and can detect multiple points of input at once, allowing for multi-touch control. PCAP screens are generally better at detecting input when the operator is wearing gloves. If there is a need to use a stylus, be aware that it will need to have a conductive material on the tip for a capacitive screen to detect it.
6. Operating temperature
When choosing a Web HMI, you may also need to consider the temperatures that it will be subjected to at the work site. Like all electronics, Web HMIs are designed to operate within a specific temperature range. For example, manufacturers may rate a standard consumer model for operation in temperatures ranging from 0º to 50º C (32º to 122º F), whereas a “wide temp” model can often sustain use in temperatures ranging from -20º to 60º C (-4º to 14 0º F).
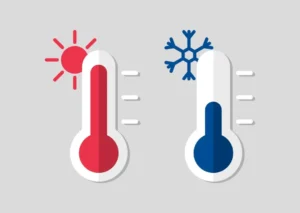
Operating Web HMIs in temperatures outside their specified range may cause display errors or other failures, therefore it is best practice to thoroughly evaluate the on-site conditions and select a panel rated for that environment.
7. Security
Using a Web HMI instead of a traditional HMI or Industrial PC comes with some significant security advantages. Because Web HMIs are client devices that do not store data locally, they are less vulnerable to data breaches through physical access.
Additionally, the centralized nature of data storage in a Web HMI setup also means that updates and security patches can be deployed more swiftly and uniformly across the entire network. This reduces the risk of vulnerabilities remaining unaddressed due to neglected updates on individual devices.
Because all user interactions with the Web HMI are mediated through a web server, there are opportunities to implement robust, centralized security measures such as multi-factor authentication and end-to-end encryption, further enhancing the overall security posture of the network.
8. Support resources
Choosing the right Web HMI involves more than just technical specifications. Availability and quality of support resources also play a pivotal role in the Web HMI’s long-term performance and user satisfaction.
Documentation
Comprehensive and accessible documentation is the first line of support for any device. Detailed manuals, installation guides, and troubleshooting resources are indispensable for both initial setup and ongoing maintenance. These resources should be clear, thorough, and tailored to various skill levels. This ensures that users can effectively operate and maintain the Web HMI, regardless of their level of expertise.
Technical support
If issues arise during installation or operation, having convenient access to technical support resources can enable you to troubleshoot and resolve issues swiftly. Manufacturers should provide multiple channels of support, such as phone, email, and chat services, staffed by knowledgeable technicians. The availability of quick and efficient technical assistance minimizes downtime and ensures smooth operations, which can be crucial in time-sensitive environments.
Warranty
Adding new equipment to your site can require a significant investment of time and money, so it is important to know that your devices are covered by a robust warranty in the event of a hardware failure. Make sure to choose a manufacturer that provides warranty terms for their devices so you can rest easy knowing that you are covered in the event of a hardware failure.
9. Certifications
It is important to consider various certifications that indicate compliance with safety, quality, and environmental standards for a new device. These certifications serve as benchmarks for reliability and performance in different environments and applications. Understanding what each certification represents can help in choosing a device that meets specific regulatory and operational requirements.
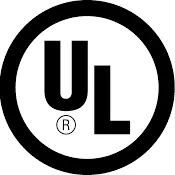
UL (Underwriters Laboratories)
UL certification signifies that the device meets stringent safety standards, primarily for the North American market. This certification indicates that experts have tested the device to ensure it complies with safety-related requirements, including risks like fire, electric shock, and related hazards.
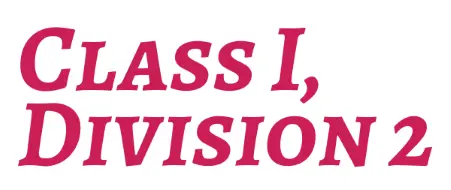
Class I, Div 2
The UL organization issues this certification specifically for devices used in hazardous locations. Class I, Div 2 certified devices are designed to operate safely in environments where flammable gases or vapors may be present under abnormal conditions.
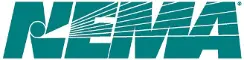
NEMA (National Electrical Manufacturers Association)
NEMA ratings define the types of environments in which an electrical enclosure can be used. A device with a NEMA rating is certified for protection against factors like dust, water, and corrosion, making it suitable for various industrial conditions.
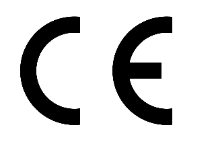
CE (Conformité Européenne)
The CE mark indicates that the device complies with the necessary European Union regulatory requirements, particularly in terms of health, safety, and environmental protection. It is mandatory for products sold within the European Economic Area.
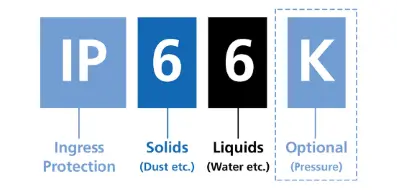
IP (Ingress Protection)
IP ratings, denoted as IP followed by two digits, indicate the level of protection a device offers against solids and liquids. The first digit represents protection against solid objects, and the second digit represents protection against liquids. Higher numbers mean better protection.
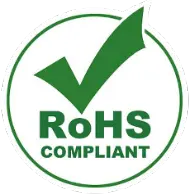
RoHS (Restriction of Hazardous Substances)
RoHS compliance means that the device does not contain specific hazardous materials banned by the European Union, such as lead, mercury, and cadmium. This certification is important for environmental protection and health safety.
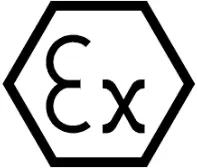
ATEX (Atmosphères Explosibles)
ATEX certification applies to equipment intended for use in explosive atmospheres in the European Union. It ensures that the device is designed to prevent ignition and can safely operate in potentially explosive environments.

FCC (Federal Communications Commission)
The FCC certification is relevant in the United States and indicates that the electromagnetic interference from the device is under limits approved by the Federal Communications Commission. This is important for preventing undue interference with other electronic devices.
These certifications ensure that a device is suitable and safe for specific applications and environments. This not only ensures compliance with legal standards but also guarantees that the device will perform reliably and safely under the designated conditions.
Contact us
Would you like to know more? Our friendly and knowledgeable sales team can connect you to the resources you need. For information on pricing, availability, and more, send an email message to sales@maplesystems.com, or contact our team by phone at (425) 745-3229.
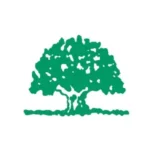
About the Author